Introduction
Carbon/carbon (C/C) composites are critical materials in high-temperature and high-stress environments, such as aerospace braking systems, rocket nozzles, and industrial machinery. Their unique combination of lightweight properties, thermal stability, and mechanical strength makes them indispensable for advanced engineering applications810. This article explores groundbreaking advancements in the
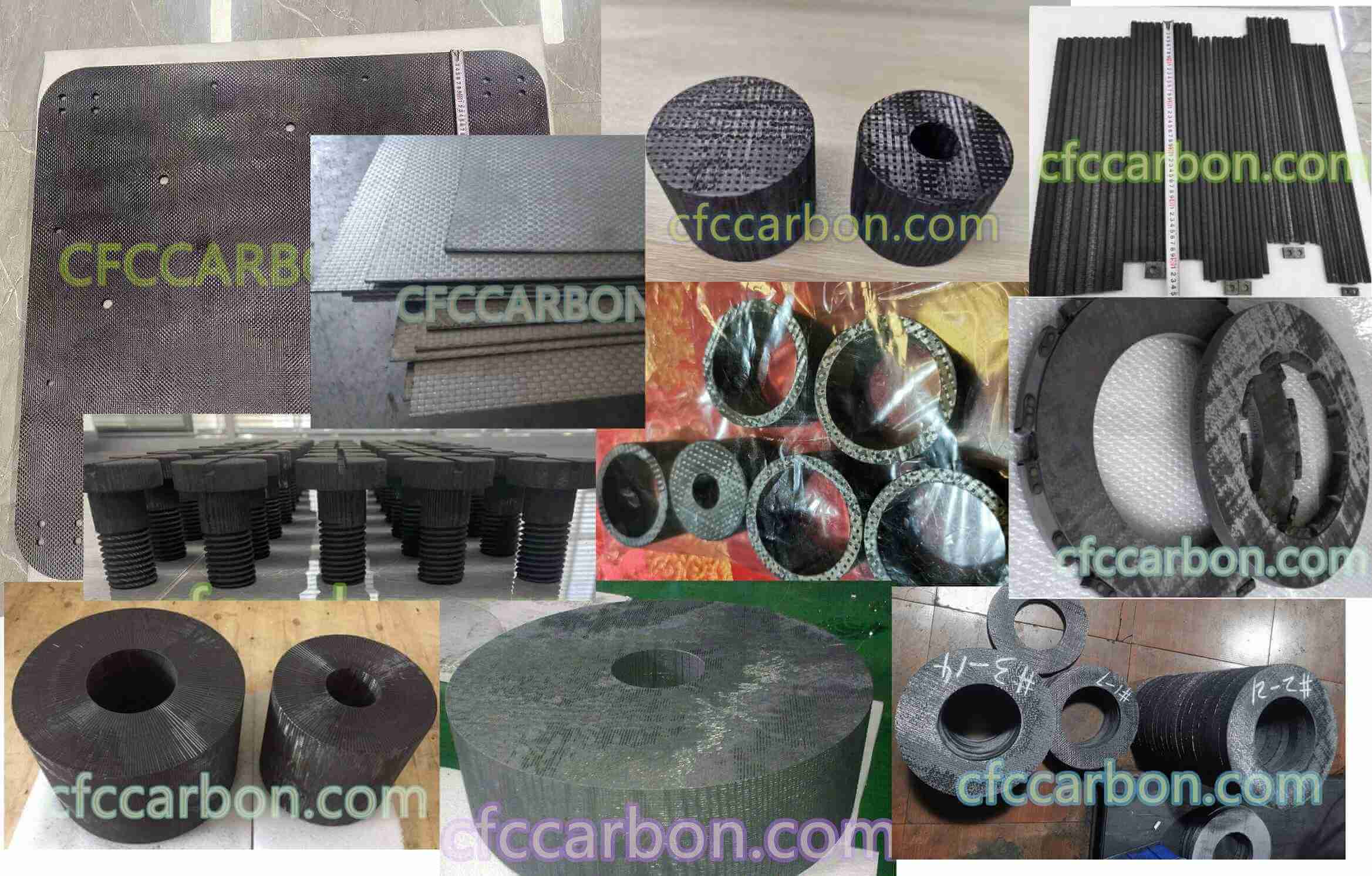
carbon fiber composite material manufacturer in China(1)
tribological behavior of fast-carbonized C/C composites, focusing on post-treatment methods that significantly improve wear resistance and friction control.
Key Innovations in Fast Carbonization
Traditional carbonization processes for C/C composites often involve slow heating rates (1–100°C/min), limiting scalability and efficiency. Recent breakthroughs at CFC Carbon utilize ultra-fast carbonization at 1000°C/min, drastically reducing production time while maintaining structural integrity513. This method preserves the composite’s porosity and fiber-matrix bonding, critical for tribological performance under extreme loads.
-
Density & Porosity Optimization: Fast-carbonized composites exhibit a 15–20% reduction in open porosity compared to conventional methods, enhancing wear resistance.
-
Cost Efficiency: Eliminating multi-step re-impregnation reduces manufacturing costs by 30%.
Post-Treatment Strategies for Superior Tribological Properties
To further enhance performance, CFC Carbon employs advanced post-treatment techniques:
-
Re-Impregnation with Carbonaceous Additives:
-
Impregnating composites with pitch/carbon black or pitch/mesophase pitch precursors reduces wear rates by 50% while maintaining friction coefficients (COF) of ~0.45.
-
This method fills microcracks and improves interfacial shear strength between fibers and the matrix.
3D 4D carbon fiber composite material manufacturer factory -airplane brake disc plates sheets U L profiles-2D(s)
-
-
Liquid Precursor Modification:
-
Doping precursors with nanoparticles (e.g., TiO₂) enhances boundary lubrication, reducing COF variability under high loads (20–80 N).
-
Experimental Results: Wear and Friction Analysis
Testing conducted on pin-on-disc tribometers under boundary lubrication revealed:
-
Wear Rate Reduction: Fast-carbonized composites treated with pitch additives demonstrated wear rates 50% lower than untreated samples5.
-
Friction Stability: COF remained stable (0.40–0.45) across varying loads (5–20 N) and sliding speeds (0.4–2.4 m/s).
-
Surface Morphology: SEM analysis showed smoother wear tracks and reduced abrasive damage due to optimized fiber-matrix adhesion10.
Applications in Extreme Environments
-
Aerospace: C/C composites are ideal for brake systems and heat shields, where thermal conductivity (>100 W/m·K) and oxidation resistance are critical.
-
Automotive: Lightweight drive shafts and suspension components benefit from the composite’s high damping capacity and fatigue resistance.
-
Industrial Machinery: Self-lubricating properties minimize maintenance in high-load bearings and seals.
Challenges and Future Directions
While fast carbonization and post-treatment offer significant advantages, challenges remain:
-
Multi-Factor Coupling: Long-term performance under combined thermal, mechanical, and oxidative stresses requires further study.
-
Cost-Effective Scaling: Industrial adoption depends on reducing raw material costs, particularly for high-purity carbon fibers.
Future research at CFC Carbon will focus on AI-driven process optimization and nanostructured coatings to enhance tribological durability.
Conclusion
The tribological advancements in fast-carbonized C/C composites position them as a cornerstone material for next-generation engineering. By integrating rapid manufacturing techniques with innovative post-treatments, CFC Carbon delivers solutions that outperform traditional materials in wear resistance, thermal stability, and operational efficiency. Explore our C/C composite product line for tailored applications in demanding environments.