Evaluation of the “correction” for the initial deflection of a plate with dimensions ~1.0 m, within the limits of the sum of m and n from 1 to 5, Ex ~10,000 Mpa, shear modulus G12 ~2000 Mpa, wcorrected ~h~ 0.006m, gives a specific load required for “correcting” warping of a single plate, ~1 Mpa. With corrected deflection of 0.03 m 5.2 Mpa is required. The “correction” increases to a third power with an increase in plate thickness proportional to the corresponding increase in its bending stiffness.
The uniformly distributed load should be markedly lower than the material strength limit (with the variation coefficient provided above for strength limit in bending the safety factor is not less than 2) and at quite a high level in order that during exposure at the temperature limit relaxation will be possible for a considerable part of the external load of carbon material. The duration of exposure in relation to plate charge warm-up scheme conditions and taking account of results presented in Fig.6, is ~3600 sec. For the central area of a thin-walled plate taking account of data of fig.6 and the model of loading a freely supported plate it is possible to estimate the limiting load q0 by an equation
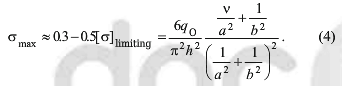
equation-4
Another technical version of correcting geometry of such a large charge may be tightening a small collection of warped plates in graphite plates with graphite bolts. Here the limiting load on the section of a graphite bolt may also be evaluated from the model presented.
During HTT of cylindrical, and other closed billets of volumetric shape creation of an induced mechanical load for restoring at high temperature (up to 2200°C) a prescribed geometric shape for solid materials is almost impossible. In this case an effective production method is use of carbon holders. The thickness of a holder should be sufficient in order that its cylindrical stiffness exceeds the bending stiffness of the wall of a billet being treated. Normally this condition is realized with a graphite holder thickness of more than 30 mm and a thickness of billet being treated of 3-8 mm. Here it is necessary that in the treatment temperature range, with which it is possible to observe arbitrary deformation of a billet being treated, expansion of the holder and its elongation over the diameter exceeds that of a composite material being treated. The contemporary carbon industry provides solution of this problem of production of a number of structural graphite and carbon composites, differing by an order of magnitude in LTEC.
Data are presented in Fig.7 for effective elongation of carbon composites during primary heating in the HTT process and possible shaping of carbon-graphite and composite materials in relation to temperature. As may be seen, widely known graphites of grades GMZ and EG-0 may be used for stabilizing the geometric shape of billets of composites based on carbon cloth from viscorse, and based carbon high-modulus threads. For billets of carbon composite based on carbon high-modulus cloth during HTT primary heating it is desirable to prepare holders, for example from lightweight graphite grade VK20 or lightweight carbon short fiber composite TKM. A similar lightweight composite fitment has been used in manufacturing objects with a height of more than 5000mm. At the same time, it is apparent that in each specific case in order to organize production of objects from CCCM it is necessary to carry out special dilatometric studies for the change in shape of carbonized carbon composite and choice of carbon materials for manufacturing shaping holders. Without optimum choice of a pair of materials inadequate efficiency of controlling geometry or extension of an object with breakage over the generating line is possible.
Internal stresses are accumulated during the whole high-temperature treatment and are the main physical factor capable of leading to irreversible loss of consumer usefulness of carbon-carbon billets and objects as a result of this production operation.
Restoration of distorted geometric shape of plates of carbon composites may be carried out effectively by action of an external mechanical load at a level less than 20-45% of the strength limit for carbonized material in the temperature range of temporary plasticity from 1900 to 2200°C. Restoration of a distorted geometric shape for cylindrical components of carbon composites may be carried out successfully with use of a graphite holder, having and average material LTEC providing elongation over the length of a circle, exceeding the level of elongation of a composite billet during primary heating.