It may also be seen from data of Fig.6 that effective relaxation of an external stress may be accomplished with an original proportion of it if not less than 0.3-0.45 of the ultimate strength. From this it is possible to make an assumption that prevention of plate warping with respect to shape, shown in fig.2, is accomplished by application of an external load, which would be adequate for intentional deformation. The level of minimum external load apparently in this case within the limits noted, i.e., not less than 20-45% of the initial strength of material being teated.
A model of palte bending under action of a load, uniformly distributed over the surface of a plate, being on a free base, may be adoped from classical work.
According to there is development of warping W in a relation to the level of an initial deflection a11 in carbon-reinforced plastic as a result of action of a normal stress s in the plane of a plate in relation to action of compressive force N, initiated by predominance of shrinkage of binder over expansion of filler Nx, or anisotropy of the composite reinforcement scheme Nx, σ:
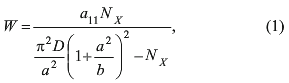
6-1 file
within which either Nx,β=(αbinder-αfiller)△TEcomposite, or Nx,σ=σxhb=-vy,xαx△TExhb, where β is carbon binder effective linear shrinkage coefficient, calculated as the ratio of the change is linear dimensions to temperature difference; is LTEC; v is Possion’s ratio; △T is HTT temperature range; Ex is elasticity modulus; h,a, and b are plate thickness, length and width; D is plate bending stiffness; X and Y are coordinate system indices.
Evaluation of the degree of increase of initial deflection of a plate with a size ~1.0m, with △T ~1000°C, Ex~10,000 Mpa, v ~1.2, gives a ratio of 3-4. Here it is easy to find that the value of the compressive force may be greater than the critical value for loss of stability:
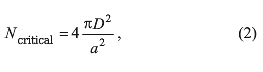
6-2-table
which leads to an irreversible shape change, as shown for actural billets and objects in figs. 1-3.
In a priactical plan for organizing manufacture from CCCM it is necessary to study the mechanism of stress initiation in a billet, and also development technical measures for restoring a prescribed geometric shape of a billet or component. A practical production method may only be carrying out carbonization and HTT under the action of an external mechanical pressure, counteracting occurrence of internal stresses.
A refined absolute value of external load may be estimated taking account of a scheme of induced “correction” of billet deformation, for example initial deflection w of a plate, with a shaping device for uniformly distributed load q0. A model of this deformation on an elastic base for an aunisotropic plate has been developed.
Prevention of deflection as a result high-temperature operations may be considered as a reverse problem:
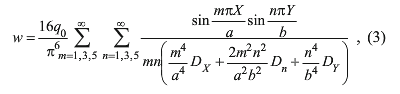
6-3 table
where w is initial plate deflection, which is obtained by experiment for measuring distortion of calculated from expression (1); q0 is load equally distributed over the surface of a billet, for hte purpose of “correcting” initial deflection; m and n are number of warping half-waves, determined by the relative stiffness Dx/Dy and dimensitons a/b of a plate.
In assembling packages of a charge the weight of the graphite load should be increased to the limit of the hearth load, permitted by furnace operating instructions, and until in areas of warping there is no shrinkage, for example commensurate with the plate thickness of all three levels.As a result of this the HTT process should as much as possible resemble thermomechanical treatment.