In order to simulate the possibility of revealed features of deformation processes for carbon substance within micro-volumes during HTT, the physicomechanical properties were studied for carbon filaments under action of a constant external load at a treatment temperature exceeding the previously reached carbonization temperature. The carbonization temperature for carbon fibers before subsequent studies of their deformation during HTT was ~800°C, as for the carbonization temperature of carbon-carbon composites, whose results are shown in figs.1-3.
Cyclic deformation curves are presented in Fig.5 for the same carbon filament specimen in the temperature range for the HTT industrial process. The constant load was about 90% of breaking load. Heating a fiber to a higher temperature was only carried out after its prior unloading. In the temperature range somewhat above 800°C there was strengthening of carbon fiber as a result of heating and soaking. Fiber elasticity modulus with approach of the test temperature to that of prior treatment of 800°C decreased with a test temperature of 20°C. The loading-unloading deformation curve develops hysteresis. Induced plastic deformation started to develop in carbon material substance. With high test temperatures the elasticity modulus increased again. Development of hysteresis ceases. The most probable explanation of this may be removal of inernal stresses with simultaneous removal of volatile components during completion of tis carbonization. In the area of 1800°C, and particularly marked at 2000°C, there is a total change in the deformation curves, i.e., strongly expressed induced plastic deformation develops. Residual deformation after unloading is 0.6-0.7%, which comprises up to 30% of the deformation limit for high-modulus carbon fibers. During primary heating again a drop in elasticity modulus is observed by 29%. During testing after cooling or with repeated heating, in contrast the elasticity modulus increases by more than double the level established after treatment at 800°C. Apparently structural transformations in carbon fiber are completed in the period of thermal cycling. This scheme of alternation of deformation processes is equivalent to that established previously in fig.4 for a composite as a whole.
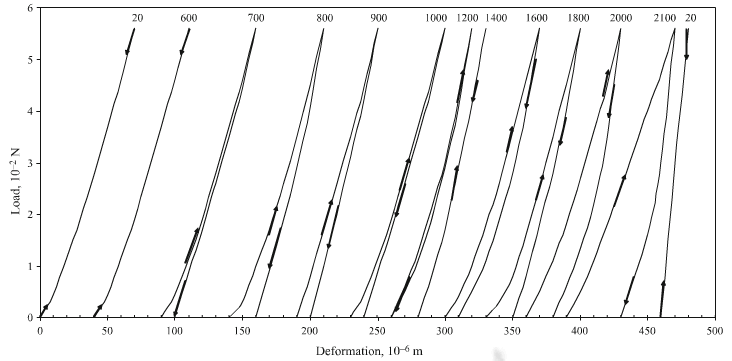
fig.5-deformation with cyclic loading of a carbon filament
Statistical results of strength and elasticity modulus tests after cooling carbon filaments showed reproduction of average values and mean square deviations. The maximum coefficient of variation for values did not exceed 30%. For carbon threads, previously heat treated up to 2200-2400°C, the strength in the temperature range from room to 2300°C increases steadily. Therefore, it may be suggested that carbon substance of test filaments during primary heating in the temperature range may entirely simulate process observed during HTT of carbon composites.
By maintaining a constant load in a fiber, its relaxation was studied in relation to time and original level of loading. Results obtained at 1900°C are shown in Fig.6. As may be seen, an external load as a result of noted
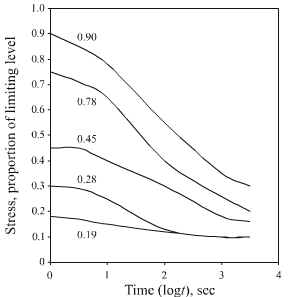
fig.6-load relaxation in carbon fiber from thread based on polyacrylonitrile
temporary plasticity of carbon material successively decreases. The rate of the process is proportional to the original value of load. The limiting level of load after its relaxation at a maximum is less than one third of the original strength. Determination if stress relaxation activation energy for carbon fiber substance at this temperature gives a value from 62 to 104 kJ/mole. This level correspond to deformation molecular processes and signifies predominance of rheological processes of movement of substance mass, and development of its plasticity. It follows from results presented in figs.5 and 6 that in the primary heating temperature range around 1900°C stress relaxation within a carbon composite system may lead to irreversible shape changes. In the direction of a carbon fiber changes have an elongation mode. Finally this should lead to distortion of the original billet geometric shape. In the case of restrained deformation with closure of a shell or conditions of plate continity, development os shell out-of-roundness or plate corrugation might be expected.