Silicon Carbide Graphite Crucible, also known as graphite clay crucible. Because its main content of this crucible are silicon carbide (SiC) and graphite. Mainly used for melting copper, aluminum and other common metals. The cost of this kind of crucibles is relatively low, with large capacity of molten metal. The crucible molding method is mainly pressure forming method.
A Routine operation
1. Inspection: Be sure to check the crucible before use to prevent any possible damage to ensure that the crucible intact. Crucible must be
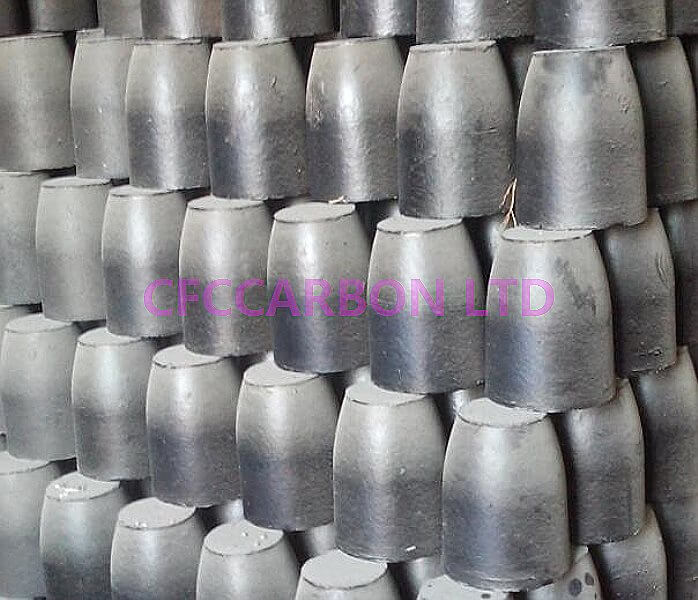
sic graphite crucibles
checked at any time during use, including: crucible wall wear, damage, to ensure that the crucible is not sick work.
2. Installation: A, pre-installation check coil mud packing is in good condition, the shape is similar to round, if necessary repair and fully dry.
B, close to the coil of mud to fill a layer of smooth surface of the media, such as mica or glass cloth, and to ensure that the overlay in the same direction.
C, installation of ground protection and the installation of ground.
D, in the bottom of the furnace by adding 3 to 4 inches of bedding, and gently ramming, each layer to get rid of the gas and for the next layer before leveling the ramming of the litter.
3. Shot: Remove metal spatter, to avoid the use of local overheating and damage to the coil.
4. Note:
A, on the coil center, may produce hot spots and cracks.
B, the bottom of the crucible can not be lower than the lowest coil.
C, check the crucible height and level, if necessary must be adjusted.
D, with the wooden wedge crucible will be fixed in the center of the furnace coil.
E. Add dry, vibrating backing fine powder (must be non-sintered) between the crucible and the furnace wall, one-tenth the diameter of the crucible.
F, ramming to the top of the crucible from about 50 ~ 75MM, should be used to seal the top of the plastic crucible, and can be made of plastic ventilation holes to help dry.
Second, the use of crucible
1. Preheating of the crucible
A, crucible preheating is to extend the life of one of the crucible aspects, in many cases, the crucible is damaged during the preheat, the damage before the molten metal is not obvious.
B, when curing furnace refractories, do not heat the crucible, or temperature changes will make the binder oxidation.
C, the crucible for the first time heating, every 10 minutes, an increase of 20% power, until the optimal operating power.
2. The feeding of the crucible
A, the large metal ingots perpendicular to the crucible to ensure that the ingot and the crucible wall between the appropriate gap.
B. Do not wedge the cold metal ingot horizontally into the crucible because the expansion of the metal during heating can cause the crucible to rupture.
C. In no case should the ingot be thrown into the crucible, as this will damage the rim and the crucible wall. Metal ingots or other heavy metal blocks should be carefully placed in the crucible using special pliers.
D, metal ingots and large pieces of waste must be added before drying, metal materials should be loose into the bottom of the crucible, it is best to join the small pieces of material at the bottom of the crucible for large metal ingot bedding.
E, leaving some liquid metal in the crucible, can accelerate the melting of metal, to avoid large metal ingots added to a small amount of liquid metal, which will cause chilling or solidification of the metal, prompting the crucible immediately rupture.
F, when the furnace power failure, the crucible must be completely empty. Otherwise due to different expansion rate will cause the metal material solidification in the crucible, in the next heating, leading to crucible rupture.
G, if the join is a liquid metal, to avoid the folder too full. It is important to note that the ingot can not be thrown into the crucible because the sharp edges of the ingot can damage the crucible wall.
2. Dusting, degassing and refining
A, the role of additives for the molten metal
1, the formation of protective cover to avoid oxidation.
2, to help remove gas and solid impurities.
3, adjust the alloy chemical composition, improve the casting performance and basic organization.
4, to ensure that slag soft, fluffy, but not hard, sticky.
B, refining slagging method
1, according to the manufacturer’s instructions, the use of additives. Only add the minimum amount required to complete the slag. In order to extend the life of the crucible, only in the casting before adding refining agent, crucible should be at least 1/3 volume of molten metal.
2, at the end of each day, should clean the crucible, remove sticky residue. Because the unused scavenging agent will penetrate into the slag and diffuse into the crucible, increasing the risk of erosion by the scouring agent.
3, the crucible and refining agent reaction speed is proportional to the temperature, crucible overheating will seriously shorten the service life.
4, the flow of good refining agent will be through the crucible wall, in oxygen and combustion gases, from the outside attack crucible, glazed bubbles and large deep pit is a symbol of such erosion.
5, the crucible outside the refining agent overflow or splash will have the same effect.
C, casting method
1, once the metal liquid to achieve the required casting temperature, and as required deslagging and degassing, it should be cast as soon as possible.
2, does not recommend the liquid metal in the crucible for a long time insulation, which will shorten the life of the crucible and reduce the quality of metallurgy.
3, so that the crucible in the casting position, continue to heat, is not good operation. This will lead to inhale, metal burn, crucible wall corrosion is uneven, early damage.
4. When pouring a small amount of metal from a large tilting crucible furnace, the crucible should be returned to its vertical position between the next pouring.
5, special attention: When the crucible containing molten metal, the crucible handling equipment must be strong and has been appropriate to support the bottom of the crucible.
3, the formation of slag
A, slag generated in the metal pool, in order to eliminate the liquid metal contaminants, oxides and inclusions, refining, part of the slag adhesion in the crucible wall.
B, just formed, the slag is very soft and easy to remove. When the slag remains, they become extremely hard and difficult to remove.
C, crucible wall multi-layer slag will inhibit the crucible performance, but also crucible damage in advance one of the most common reasons.
4, cleaning methods
A, the correct removal of slag is very important.
B, after the first heating, when the crucible is still hot, it should be completely scraped slag.
C. Then, at the end of each day’s work, clean the crucible.
related news /articles:
Silicon carbide graphite crucible (3)-SiC graphite crucible
Silicon carbide graphite crucible (1)-standard type
Silicon carbide graphite crucible (2)-Clay graphite crucible