Upon irradiation, the lattice structure of graphite changes due to the production of interstitial atoms and vacancies. Interstitial atoms move between layer planes and can be mobile at very low temperatures. On the other hand, vacancies have been assessed to be mobile at temperatures greater than 1000K. Therefore, to enable partial annealing of the damage, temperatures higher than the irradiation temperature should be induced, assuming that interstitial atoms mobile up to that temperature have already been placed back in the lattice, or pinned at grain boundaries. To investigate this annealing process, thermal strain measurements of the specimens were made using a dilatometer.
Figure 2 shows thermal strain measurements of un-irradiated and irradiated POCO graphite at 0.084 DPA as a function of temperature
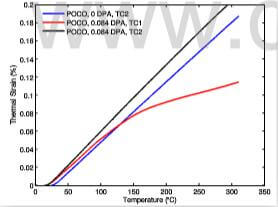
fig.2-dimensional-changes-in-un-irradiated-and-irradiated-graphite-over-two-thermal-cycles
over two thermal cycles. Upon the first thermal cycle to 300°C, the irradiated specimen shows significant decrease inthermal expension. However, in subsequent cycyles, the graphite appears to have recovered its un-irradiated expansion characteristics and shows a slightly higher thermal expansion than the control specimen. This trend is qualitatively similar across all the graphite grades. The irradiation temperature, which is about 150°C, can also be inferred from Fig.2. The experimental results give further insight into the interstitial atom annealing and damage reversal process. Similar damage reversal phenomena were observed with the 3D C/C composite, exposed in both water and argon environments during the experiment. Results shown in figs. 2 and 3 confirm that significant thermal property changes can occur at low DPA levels while damage reversal is possible at annealing temperatures higher than the irradiation temperature, thus providing practical information on optimal operating temperature of future targets.
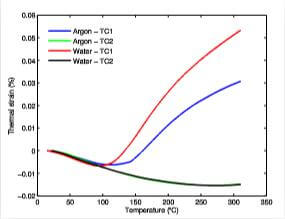
fig.3-thermal-cycling-following-irradiation-of-3D-CC-composite-specimens
Mechanical testing:
Tensile tests were performed on irradiated graphite specimens to investigate the effect of radiation damage on tensile strength and elastic modulus, E. The tensile test results for IG-430 graphites, irradiated at different DPA values, are shown in Fig.4 and indicate increased elastic modulus and tensile strength than the un-irradiated specimen. However, no distinct dependence on DPA is observed, mainly due to the interrelation of DPA and irradiation temperature. As described in the previous subsection, the irradiation temperature dictates the extent of damage annealing.
Figure 5 shows the damage reversal process of irradiated POCO graphite at 0.07 DPA due to annealing at 350°C. Both the elastic modulus and the tensile strength revert back to the un-irradiated state. Tensile tests of 3D C/C composites did not provide reliable data because the specimens consistently slipped or failed at the head. Further studies will employ a bending test fixture to evaluate the flexural strength of the 3D C/C composite specimens.
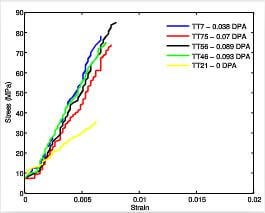
fig.4-stress-strain-curves-for-irradiated-IG43-at-varying-DPA-levels
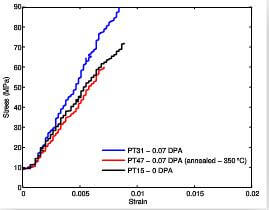
fig.5-annealing-effect-on-tensile-properties-of-graphite
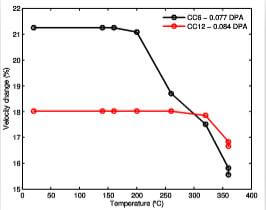
fig.6-ultrasonic-velocity-recovery-in-irradiated-and-annealed-C2020-specimens
Ultrasonic tests were performed to further quantify the change in elastic modulus due to irradiation and post-irradiation annealing. The wave velocity, which is proportional to the elastic modulus, was estimated by measuring the travel time and propagating length of the waves through the specimens.
Figure 6 shows velocity meansurements for C-2020 as a function of temperature, with specimen CC12 previously annealed at 310°C and CC6 unannealed. As seen for temperatures at and below the irradiation temperature, the percent velocity change remained constant for both specimens. However, due to interstitical mobilization above the irradiation temperature, a downward trend is exhibited by CC6 after 150°C while CC12 remained unchanged until about 310°C. These results again confirmed changes in elastic modulus due to low DPA irradiation and its annealing-induced restoration.
Ultrasonic tests were difficult to apply to 3D C/C composites because the array and layers of fibers scatter and diffuse the ultrasonic pulse, which has a wavelength smaller than the diameter of each fiber.