Introduction
Carbon-carbon (C/C) composites are indispensable in aerospace and high-performance braking systems due to their exceptional thermal stability, low density, and friction properties. However, catalytic oxidation triggered by alkali-based runway de-icers, such as potassium acetate, has emerged as a critical challenge, accelerating material degradation and shortening brake lifespan214. This article explores cutting-edge protection mechanisms to mitigate catalytic oxidation, ensuring the longevity and reliability of C/C composite brakes.
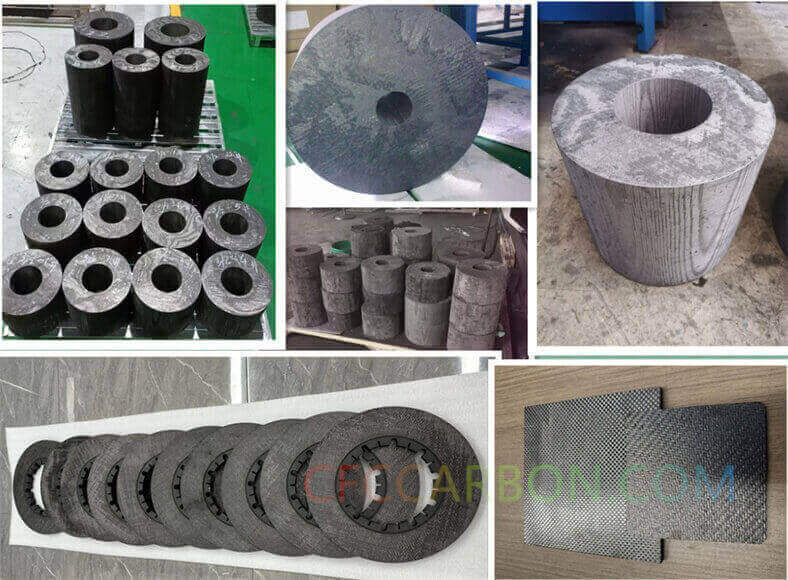
3D 4D carbon fiber composite material manufacturer factory -airplane brake disc plates sheets U L profiles-2D(s)
1. Material Quality Enhancement: Reducing Defects and Porosity
Improving the intrinsic quality of C/C composites focuses on minimizing defects and porosity, which serve as pathways for oxygen infiltration. Advanced manufacturing techniques, such as chemical vapor infiltration (CVI), optimize matrix densification, reducing porosity to below 10% while maintaining structural integrity17. Heat treatment at extreme temperatures (up to 2623°C) promotes graphitization, converting amorphous carbon into crystalline graphite—a structure less reactive with oxygen. However, excessive graphitization risks fiber embrittlement, necessitating a balance between oxidation resistance and mechanical strength.
Recent innovations in precursor selection and fiber alignment have further refined composite homogeneity, reducing active carbon sites vulnerable to catalytic attack. For instance, polyacrylonitrile (PAN)-based fibers, processed via needling and controlled carbonization, yield composites with enhanced oxidation resilience.
2. Inhibitor Integration: Boron and Phosphorus Compounds
The addition of oxidation inhibitors directly into the composite matrix has proven effective in neutralizing catalytic agents like potassium and calcium.
-
Boron-Based Inhibitors: Boron oxide (B₂O₃) acts as a dual-phase protector. At temperatures below 1500°C, it forms a viscous glass layer that seals surface cracks and poisons catalytic sites. When combined with silicon carbide (SiC) coatings, boron’s protective range extends to 1400°C, making it ideal for high-stress scenarios like aborted take-offs314. Substitutional boron doping further enhances graphite crystallinity, redistributing π-electrons to lower the material’s Fermi level and inhibit oxygen chemisorption. However, boron’s dual role—acting as both inhibitor and catalyst at low concentrations—requires precise dosage control.
carbon fiber composite material manufacturer in China(1)
-
Phosphorus Compounds: Organophosphates, such as methyl-phosphoric acid, form stable C-O-PO₃ bonds on carbon surfaces, blocking alkali metal mobility. Studies demonstrate that phosphorus-treated composites suppress calcium-induced oxidation by 90% and reduce potassium’s catalytic activity by 50%314. X-ray photoelectron spectroscopy (XPS) reveals metaphosphate barriers physically isolate catalysts, preventing interfacial contact with carbon fibers even at 1000°C.
3. Protective Coatings: Multi-Layered Barriers
Coatings serve as the first line of defense against oxygen and catalytic agents.
-
SiC and Aluminophosphate Coatings: Silicon carbide (SiC) coatings, applied via chemical vapor deposition (CVD), create a dense, oxidation-resistant layer. Aluminophosphate coatings further enhance protection by forming a self-healing glass phase at high temperatures, filling microcracks and pores1617. For instance, C/C-SiC brake discs tested in high-speed trains (350–420 km/h) exhibited minimal oxidative wear due to synergistic SiC-matrix interactions.
-
Hybrid Coating Systems: Multi-layered designs, such as B₂O₃-SiO₂ composites, combine crack-sealing and thermal stability. These systems are critical in extreme environments, such as aircraft brake surfaces exposed to 1400°C during emergency stops.
4. Industry Applications and Future Directions
Leading manufacturers like CFC Carbon Co., Ltd. leverage these strategies to produce next-generation C/C-SiC composites for aviation and energy sectors. Their patented “solid-liquid” infiltration process integrates inhibitors and coatings in a single cycle, reducing production costs by 30% while achieving 95% densification.
Future research aims to optimize inhibitor synergy—for example, combining boron-doped matrices with phosphorus-rich coatings—to address alkali mobility at ultra-high temperatures. Additive manufacturing and AI-driven microstructure modeling are also emerging as tools to design composites with gradient porosity and tailored oxidation resistance.
Conclusion
The fight against catalytic oxidation in C/C composites hinges on multi-faceted strategies: material refinement, inhibitor engineering, and advanced coatings. As runway de-icers evolve, so must protective technologies to ensure aerospace safety and sustainability. Collaborative efforts between academia and industry, exemplified by CFC Carbon Co., Ltd., will drive innovations in this critical field.
For more details on C/C composite technologies, visit www.cfccarbon.com.
related news /articles:
Protection Mechanisms Against Catalytic Oxidation in c/c Composites (2)
Protection Mechanisms Against Catalytic Oxidation in C/C Composites (3)
Inhibition oxidation of carbon-carbon composites (1)
The use of inhibitors to provide oxidation protection to carbon-carbon composite