Carbon/carbon composites in the true sense, cover a large range of materials with the targeted properties. The properties of interest are strength and stiffness, fracture toughness, frictional properties, thermal conductivity and resistance to oxidation at high temperatures. The operating mechanisms for these properties are quite different, especially in such multiphase composite materials. The mechanical properties of the constituents and their volume fraction, boding, and crack propagation mechanism control the mechanical properties of the composites, whereas thermal properties are governed by thermal transport phenomena. Moreover, the constituents, both reinforcement and matrix, are likely to undergo a change in properties during processing as influenced by heat treatment temperature, differential dimensional changes, thermal stresses etc. All these factors influence the ultimate properties of the composites. It is difficult to cover completely all these aspects in this article. However, a general trend of the most fascinating properties of carbon/carbon composites are given below.
- Mechanical properties of carbon-carbon composites
The strength and fracture of carbon/carbon composites are governed by the Cook-Gorden theory for strengthening of brittle solids, which states that if the ratio of the adhesive strength of the interface to the cohesive strength of the solid is in the right range, a large increase in strength and toughness of otherwise brittle material is achieved. Extensive work has been done in achieving highest possible translation of fiber properties in carbon/carbon composites. Composites with strong fiber/matrix bonding fail catastrophically without fiber pull-out while those with controlled interface fail in mixed tensile cum shear mode exhibiting high strength. Numerical values of the mechanical properties of the composites are dependent on the fiber architecture and the direction of measurement of the properties w.r.t. fiber orientation etc. as shown in figure 7. Other architectures and fiber lay-
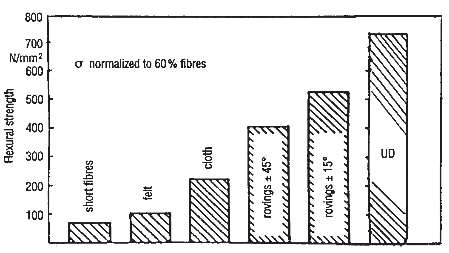
stength of carbon-carbon composites with fiber orientation
ups have similar effects and the values lie in-between. Similarly, these composites exhibit a range of high fracture toughness and good creep and fatigue resistance. When subjected to high temperature testing, carbon/carbon composites have been found to exhibit about 10-20% increase in mechanical properties at 2000C under inert atmosphere. However, in air, the properties drop down to 10-20% depending on the temperature and time e.e. the weight loss. Carbon is a stable and highly sought after material for nuclear applications. So are carbon/carbon composites. Under neutron irradiation at low fluence levels of 1021 n/cm2, these composites exhibit an increase in strength and fracture toughness by 20-30% and Young’s modulus by about 30%.
- Thermal properties of the carbon carbon composites
Carbon/carbon composites being of heterogeneous structure consisting of fibers, matrix and pores, with the first two having a variety of microstructures, estimation of their thermal transport properties becomes complex. However, carbon/carbon materials with tailored thermal conductivities can be fabricated by proper choice of constituents, their configuration, and processing conditions. A comparison of thermal conductivities of carbon/carbon composites with different fiber/matrix combinations is given in figure 8. Composites having highly
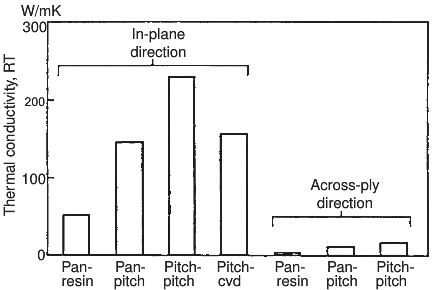
thermal conductivity of CC composite with different fiber-matrix combinations
oriented graphitic fibers or matrices or their combination, like vapour-grown carbon fibers and matrix or mesophase pitch-based carbon fibers and matrix, exhibit very high thermal conductivities of the order of 250-350 W/M.K in the fiber dtirection. Though these composites exhibit highly anisotropic character and low conductivities in transverse directions, there is always scope of improvement by varying the fiber architecture and their addition in different forms and ways. Coefficient of thermal expansion of the composites is dictated largely by the fiber orientation. It is 0-1 ppm/C in the fiber direction and 6-8 ppm/C in a direction perpendicular to the fibers.
Carbon/carbon composites, developed about three decades ago to meet the needs of the space programme, are nowadays considered high performance engineering materials with potential application in high temperature industries. Accordingly, steady growth also prevails in the civil market segment. In terms of mass consumption, the main application of carbon/carbon composites are still in high performance braking systems. New innovations still own to requirements from space industries. In general engineering sectors these are used in engine components, as refractory materials, as hot-pressed dies and heating elements, as high temperature fasteners, liners and protection tubes, as guides in glass industries etc. Some of the applications are shown in figure 9.
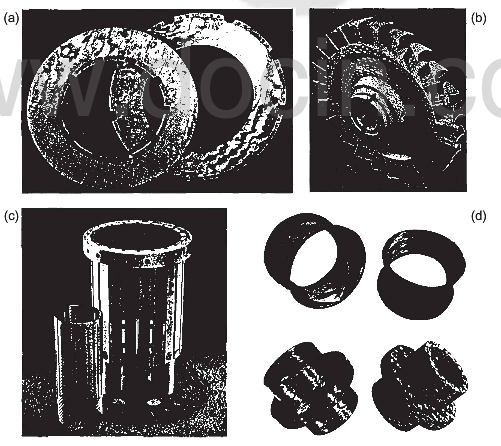
applications of carbon carbon composite-brakes discs, turbine rotor, resistance-heating elements, protection tubes and grids.
Carbon/carbon composites have great potential in energy sectors as polar plates for fuel cells, in storage batteries etc. As the technology becomes more economical a viable, more and more applications get evolved.