Fig.4 shows the photomicrographs of the C/C composites woven with axial carbon rods. Pores inside the carbon fiber preform have been infiltrated by pitch-based, in which flake-like carbon dominates. Spaces between carbon fiber bundles and spaces between fibers have been filled completely, which results in a whole composite body and a toughen fracture feature as shown in the figures.
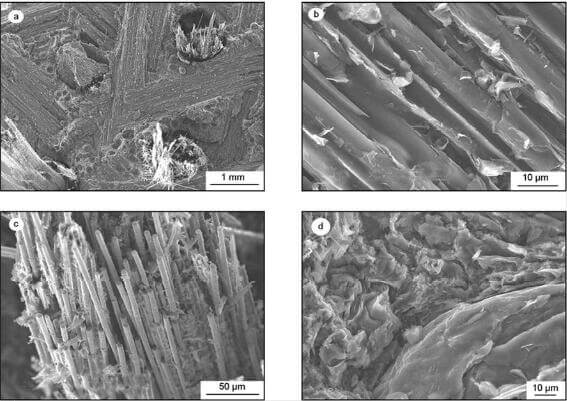
fig.4-photomicrographs-of-CC-composite-woven-axial-carbon-rods
Effect of preparation process on properties of the C/C composites:
The axial CTE has obvious influence on the thermal stress of the C/C throat insert, distribution of which directly reflects ablation resistance of the C/C composites. And the ablation resistance affects the work reliability of the C/C throat insert. So, in order to decrease the CTE and improve the ablation resistance of the C/C composite throat insert, it is necessary to optimize the preparation processes to enhance the work reliability. According to the theoretical analysis and experimental works done formerly, HTT process was adopted to the present work. Properties of the C/C composites throat insert before and after the HTT were measured and listed in Table.1. It is found from Table 1 that room temperature tensile strength decreased and the high temperature tensile strength at 2800°C keep identical after HTT. Meanwhile, the axial CTEs were reduced sharply and the ablation masses were also decreased. It is evident that HTT process could help to decrease the axial CTE without any damage to interfaces between fibers and matrix. In this process, tensile strength at room temperature decreased and there were little effects on high temperature tensile strength. The preparation process effectively decreased the axial CTE and ablation mass while keeping other properties and the work reliability of throat inserts unchanged.
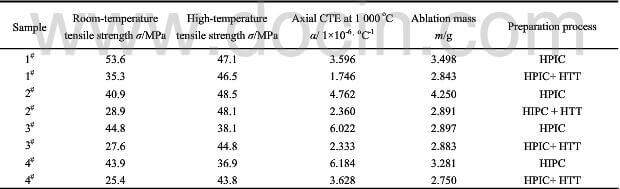
table.1-properties-of-CC-composite-before-and-after-HTT
High temperature tensile strength and fracture behaviours of the C/C composites woven with axial carbon rods:
When they were heated, thermal stress inside the C/C composites would generate, at the same time the thermo-physical properties such as CTE, thermal conductivity and mechanical properties would have a non-linear relationship with temperature. Therefore, in order to design a suitable structure for throat insert, it is necessary to investigate the mechanical properties at high temperature and fracture character of the C/C composites woven with axial rods.
Fig.5 shows the tensile stress-strain curves of the C/C composites at 2800°C. The axial tensile strength, elastic
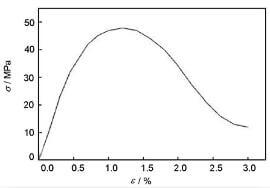
fig.5-tensile-stress-strain-curve-of-the-CC-composite-at-2800°C
modulus and fracture strain are 47.9 Mpa, 9.73 Gpa and 1.2% respectively. At 2800°C, there is no obvious brittle fracture behavior for the C/C composites. The stress-strain curves of the C/C composite can be divided into three parts. At the first part, the tensile stress-strain curve has an approximate linear relationship, illustrating and elastic strain process, in which no damage has been found for both the fibers and the matrix. At the second part, the tensile stress-strain curve is approximately a parabola relationship at the maximum stress point. With the increase of stress, some cracks would be formed and propagate in the matrix. At the last part, the fiber-matrix interfaces debonded. The destroyed matrix would have no ability to bear a load. The load was transferred to the carbon fiber, which results in the fracture of the fibers gradually. There is no sudden rupture during the whole process. FIg.6 shows the SEM micrographs of the fractured surfaces of the C/C composites. Fractured surface of the C/C composites formed at 2800°C during the tensile test is neat. In the X-Y direction, the plane vertical to the axial, delamination occurs with little fiber fractured (fig.6c and 6d). While in the Z direction, the fiber bundles have a zigzag fractured cross section with some fibers pulled out (fig.6e and 6f). Stress caused some cracks and the crack propagation did not deflect, leading finally to fracture of the material. A large size carbon layer would be formed due to the large space among fiber bundles, resulting in the increasing of the probability of interlay cracking of the weakly-bonding interface. Therefore the tensile stress-strain curve changes slowly without any steps formed by sudden fractures during the damage of the C/C composites woven with axial carbon rod.
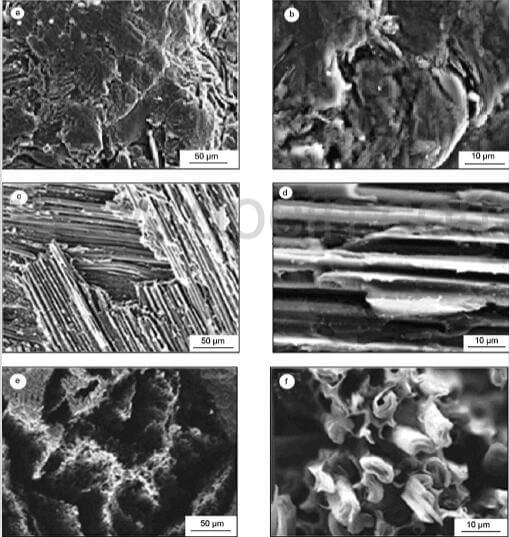
fig.6-SEM-micrographs-of-the-fracture-surfaces-of-CC-composite