A new kind of C/C composite was made to meet the requirements of the severe conditions suffered by a high performance throat-insert of a solid rocket motor using a method that includes four steps: preform preparation, pressure impregnation and carbonization, high pressure impregnation and carbonization, and high temperature treatment. The preform was made of soft carbon fiber yarns and rigid carbon fiber/resin rods, in which the carbon rods were distributed in an hexagonal arrangement parallel to the axial direction and carbon fiber yarn were laid in a plane prependicular to the axial carbon rods with a nearest inter yarn angle of 60. The influence of the main processing conditions on the key properties of these composites was investigated. It is found that the composites have excellent mechanical and thermal properties, and their ablation rates are equivalent to those C/C composites reinforced with an integral felt preform and 60% lower than those of the C/C composites woven with radial carbon rods.
The C/C composites, which possess excellent mechanical property at high temperature and ablation resistance, are ideal candidates of throat inserts in solid rocket motor (SRM). The C/C composites with an integral felt preform have low axial mechanical strength, owing to a low fraction of carbon fibers in axial direction. The C/C composites, woven with radical carbon rods, has low fraction of carbon fibers in radical direction and high erosion rates when used in high pressure combustion condition of SRMs. Therefore, it is necessary to develop a new kind of carbon fiber reinforcement structure for the high performance C/C composites to meet the severe requirements of SRMs.
The C/C composites are composed of carbon fibers, carbon matrix, interfaces, pores and micro-defects. Their mechanical properties, thermal properties and ablation resistance are affected by the carbon fibers’ weaving structures. The C/C composites reinforced by woven preforms possess better mechanical properties and flexible designability. Thus, the C/C composites for SRMs could be obtained through preform design and modification via densification.
In the present work, a new kind of 3D and 4D C/C composites have been made through the processes that include the four steps, i.e. preform preparation, pressure impregnation and carbonization, high pressure impregnation and carbonization, and high temperature treatment (HTT). Their related mechanical properties, thermal properties, and anti-erosion abilities have been characterized.
Preparation of the C/C composites woven with axial carbon rods:
The wearing technique used in the C/C composites have an advantage to make about 70% carbon fibers arranged
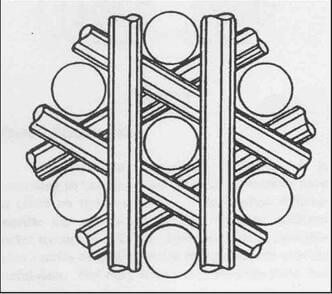
fig.1-preform-of-4D-CC-composites
in the horizontal plane prependicular to the axis of throat insert. And more radical carbon fibers are helpful to improve the ablation resistance of the resultant C/C composites. The C/C composites reinforced by this preforms have some isotropic property as compared with the C/C composites woven with radical carbon rods. Plenty of open holes and connected channels are favorable for densification when the preform woven with axial carbon rods is exployed. And the weaving process for this kind of preform is simple, efficient and easy to be realized mechanically. New preforms shown in Fig.1 and featured with 3D and 4D were made of soft carbon fiber yarns and rigid carbon fiber/resin rods, in which carbon rods are distributed regularly in the axial direction, and carbon fiber yarns are laid along the rod passages on the plane vertical to the axial carbon rods. The horizontal distribution angles for the yarns are 60°, 120° and 180°. Its density is about 0.6 g/cm3.