Description of the ablative media: Carbon/carbon composites are part of the ceramic matrix composite (CMC). They are composed only of element carbon. Nevertheless, the material shows several scales of heterogeneity with a wide range of thermochemical properties.
The composite is formed by reinforcements and a matrix as illustrated in Fig.1. The reinforcement architecture can be textile-like or show a complex multidimensional and multiaxial geometry. The reinforcements are fiber bundles or yarns made of cylinderical carbon fibers of approximately 5 μm radium. The reinforcements can be also composite materials when the fiber bundles are densigied by a matrix as illustrated in the last picture of fig.1. The matrix is deposited in the reinforcement architecture by liquid or vapor phase deposition. In these two processes, the nanotexture and nanostructure of the obtained carbon will depend on the operative conditions as well as the chemical precursors for gas-deposited pyrocarbons. The composite is treated at high temperature in order to reduce the density of micro-structural defects and to approach the graphite crystalline structure. Nevertheless, the obtained material shows significant spatial heterogeneity. The matrix has a lower coherence length of the ordered domains, which is known to be related to a higher reactivity. Two scales of heterogeneity are thus identified as illustrated in Fig.1: the micro-scale with a characteristic legnth, Iμ, of a magnitude of ten microns and the mesoscale with a characteristic length, Im, of a magnitude of few millimeters. Therefore, the macro-scale effective property is the result of a double change of scale starting from the micro-scale. Assuming the separability of these heterogeneity scales, the composite will be described as an assembly of homogeneous but distinct phases. In addition to the different carbon phases, in some of the studied materials, especially the woven ones, there is significant amount of macro-scale pores which will be taken into account by an explicit description of the pore volume.
Since the curvature radius of the parts is large compared to the scales of interest in this work, it will be neglected in the developments. Due to the industrial process of part manufacturing, the composite surface will be assumed to be perfectly flat at the initial state.
Under rocket firing conditions, the flow is highly turbulent in the core of the nozzle and the bundary layers themselves are turbulent. Computation of the mesoscale flow profile shows that the longitudinal velocity is about 1000m/s at 2mm of the ablative wall. The associated Reynolds nuber is then Rem=5*104. At the micro-scale, the Reynolds number decreases and is about Reμ=250. Modeling the turbulent momentum or mass transfer and its coupling with the surface recession is beyond the scope of this paper. In a preliminary attempt at understanding the concept of effective surface for ablative walls, we will only consider the laminar case, characteristic of the micro-scale. Moreover, compressibility of the fluid phase will be ignored.
During the ablation process, even though the macro-scale position of the ablative surface evolves due to recession, the thickness of the gasified materials is small compared to the section of the nozzle throat, and is not significantly affected. The top of the boundary layer follows the macro-scale displacement of the ablative surface. Taking into account this elolution, the model is developed in a local frame which recedes with the surface as illustrated in fig.2.
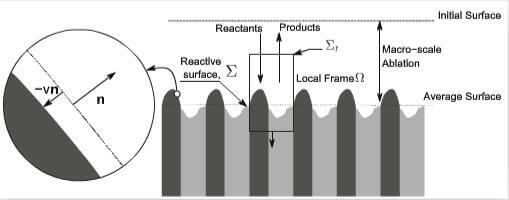
fig.2-microscale-recession-of-the-ablation-surface