The manufacturing and design of carbon-carbon composites are considered topics that require extensive treatment. This article is intended as an overview of the principles involved with carbon-reinforced, carbon-matrix composite materials.
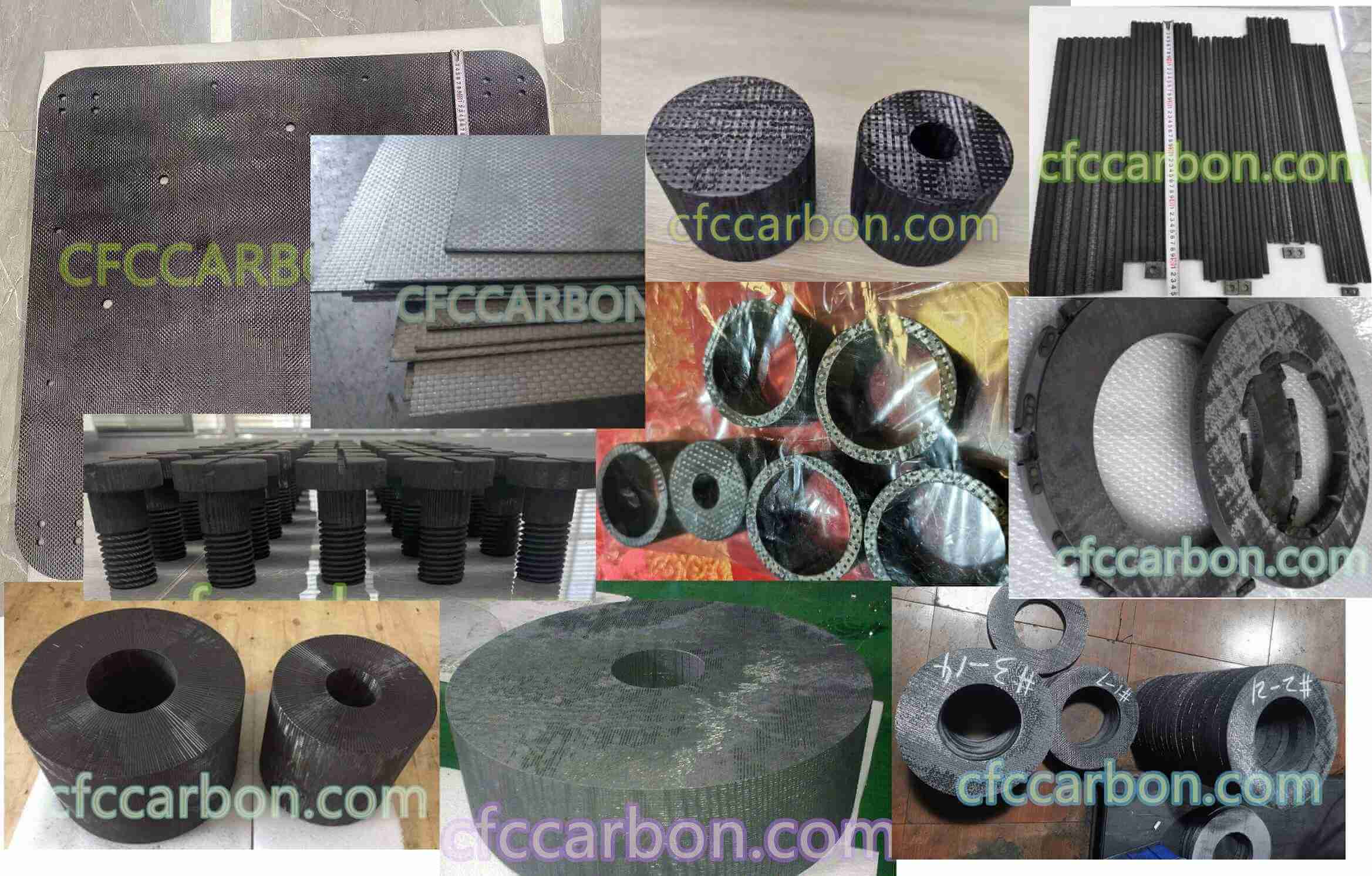
carbon fiber composite material manufacturer in China(1)
The manufacturing and design of CC composites are founded upon principles common to the design and fabrication of all composites with additional considerations specific to carbon and graphite. Principles common to the design of all composites include the following: the choice of composite preform is driven by the intended application; the reinforcing material and the matrix material must be compatible over the range of temperatures of composite will experience both in processing and intended application; and the properties of the matrix material and the reinforcement material must be such that the two materials together can interact to provide the desired composite properties. The term preform means the shape and distribution of the reinforcement in the composite. For example, a composite consisting of a uniform distribution of spheroidal silicon carbide particles in an aluminum matrix comprises a metal matrix composite having macroscopically isotropic properties. In contrast, a cured epoxy reinforced with continuous glass fibers all aligned in the same direction comprises a uniaxial composite which results in high anisotropy of properties.
Compatibility refers to chemical and thermal properties. Chemical reactivity or a large mismatch in coefficients of thermal expansion
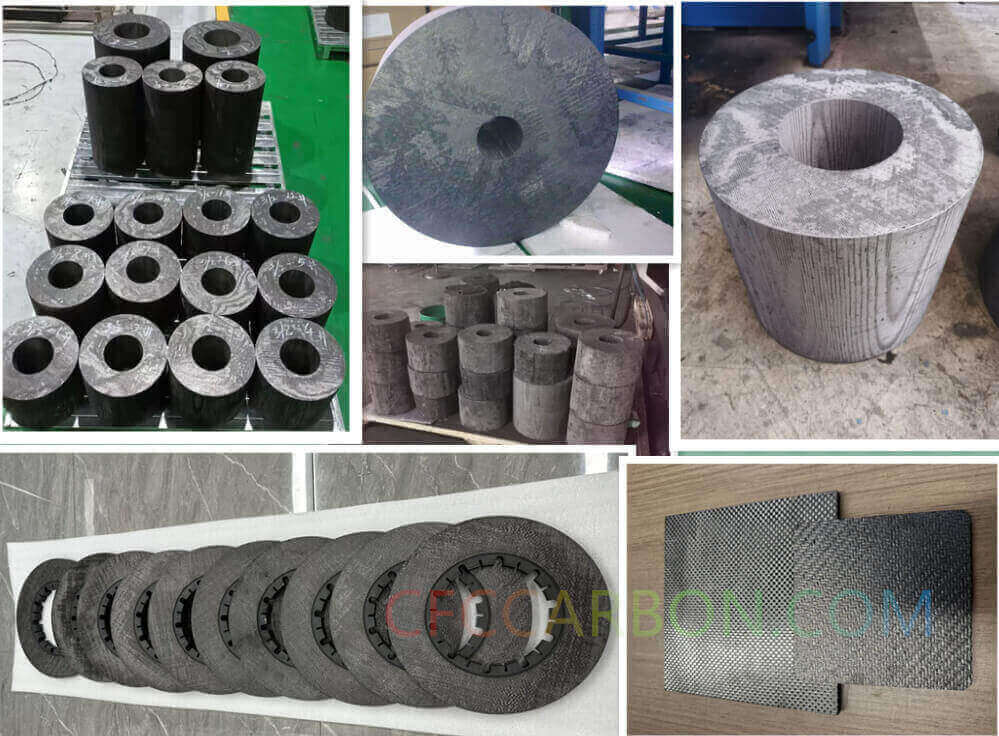
2D 3D 4D 5D carbon fiber composite material manufacturer factory -airplane brake disc plates sheets U L profiles-2D(6)
between matrix and reinforcement usually will render the materials incompatible if elevated temperatures are experienced by the composite either in processing or in use. Compatibility is typically not an issue with CC composites because of the chemical and physical property equivalence of the resulting matrix with the reinforcement upon completion of processing and because of the very low reactivities between the carbon reinforcement and the matrix precursors during processing.
Considerations specific to CC center on the unique properties of carbon and graphite. Graphite is the most refractory of materials and combines low density with desirable mechanical, thermal, and electrical properties. The low strain capability and susceptibility to thermal shock of monolithic graphite are overcome by CC composites, which retain most of the advantageous characteristics of monolithic graphite. Even though strain capabilities of CC composites are sometimes similar to monolithic graphite, load-carrying capability is significantly higher and catastrophic failure is less likely to occur.
The very low coefficients of thermal expansion exhibited by CC composites can impart unparalleled stability for applications such as space structures that experience large temperature excursions. The low CTE, low weight, high thermal conductivity, resistance to spalling, and good strength retention at elevated temperatures have made CC composite the material of choice for brakes on commercial and military aircraft. Continuous fiber-reinforced CC composites have become increasingly important to the aerospace industry as materials performance requirements for components of missiles, space structures, and aircraft have become ever more demanding.
The manufacture of CC composites entails high-temperature processing required for the pyrolysis of the matrix precursor (pitch or resin) or for the reaction of gases to form carbon matrix in chemical vapor deposition (CVD) process. cfccarbon.com
Depending upon the intended maximum use temperature, the composite may be further heat treated to graphitize the carbon matrix and to further graphitize the fiber reinforcement. Such a heat treatment, known as graphitization, chemically and thermally stabilizes the composite for use at temperatures up to the maximum temperature experienced by the composite during graphitization. Pyrolysis and graphitization are processes unique to the manufacture of carbon-matrix composites. Of these, only carbon-reinforced carbon matrix composites, or CC composite, have been important engineering materials up to now. The remainder of this article will treat CC composites exclusively.
related news /articles:
Design of carbon-carbon (CC) composite product
Development concerns (2)-impact of design requirements on C/C recommendation
Introduction of carbon-carbon (CC) material–CFCCARBON LTD
Introduction of high-temperature coatings on CC composite material