Innovative Strategies to Inhibit Oxidation in Carbon-Carbon Composites: Advancements in High-Temperature Material Science
By CFC Carbon Technical Team | May 17, 2025
1. Understanding Carbon-Carbon Composites and Oxidation Challenges
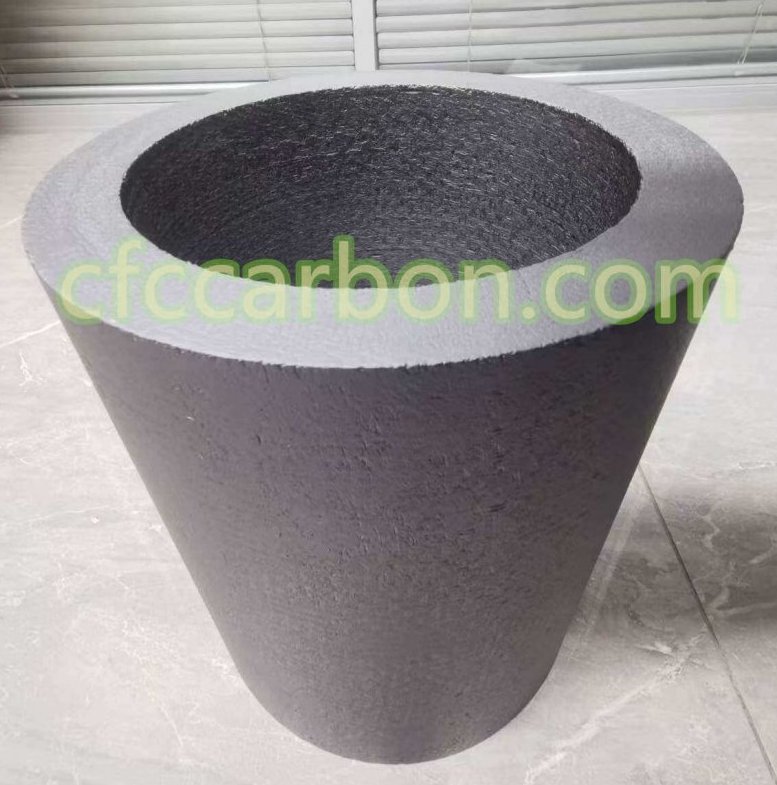
SiC coating carbon fiber composite material-CC-CFC (2)
Carbon-carbon composites (C/C) are high-performance materials composed of carbon fibers embedded in a carbon matrix. Renowned for their exceptional thermal stability (retaining strength above 2000°C), low thermal expansion, and lightweight properties, they are widely used in aerospace, braking systems, and industrial furnaces2615. However, a critical limitation is their vulnerability to oxidation at temperatures exceeding 450°C, where carbon reacts with oxygen to form CO/CO₂, leading to structural degradation.
To address this, researchers and manufacturers like CFC Carbon have developed advanced oxidation inhibition techniques. These include chemical inhibitors (e.g., boron and phosphorus compounds) and ceramic coatings (e.g., silicon carbide), which are now integral to modern C/C composite production.
2. Oxidation Inhibition Mechanisms: Boron, Phosphorus, and Beyond
Key Inhibitors and Their Roles
-
Boron-Based Additives:
Boron carbide (B₄C) and boron oxide (B₂O₃) act as physical barriers by filling surface pores and forming a glassy layer that impedes oxygen diffusion. Studies show that boron-doped composites reduce CO emissions by 80% at 700°C due to stabilized B₂O₃ layers. For instance, CFC Carbon’s high-density C/C composites (1.9 g/cm³) integrate boron-modified matrices for enhanced oxidation resistance in aerospace nozzles and brake disks. -
Phosphorus Compounds:
Phosphorus oxychloride (POCl₃) and organophosphates neutralize catalytic impurities on carbon surfaces. Research by McKee et al. demonstrated that POCl₃ adsorbs strongly at basal plane edges, blocking reactive sites and preventing etch pit formation even at 1000°C.
Synergistic Approaches
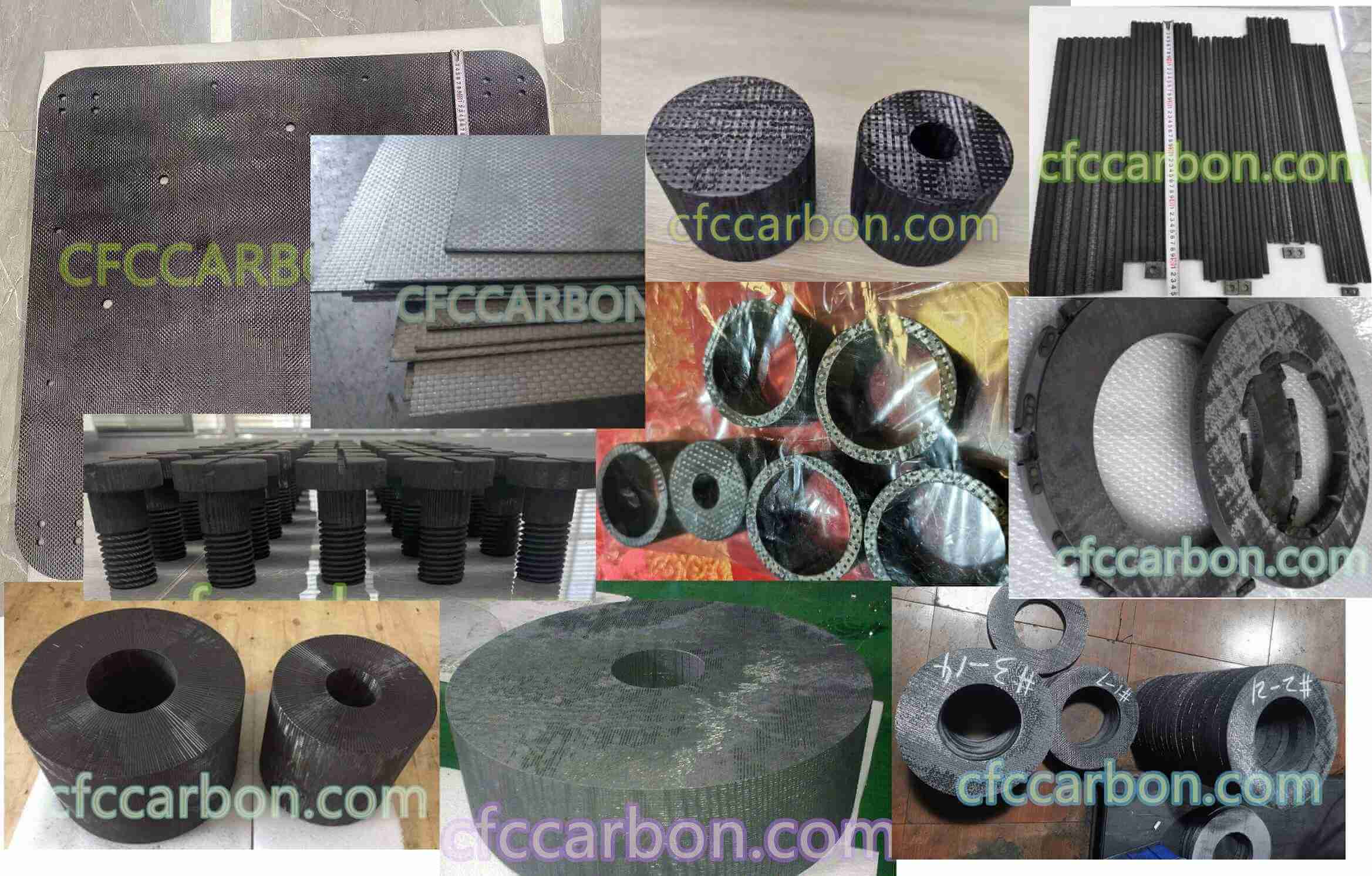
carbon fiber composite material manufacturer in China(1)
Modern solutions combine inhibitors with multilayer coatings. For example, 3D C/C composites utilize SiC coatings applied via chemical vapor infiltration (CVI), achieving >95% oxidation resistance at 1600°C in atmospheric re-entry simulations.
3. Manufacturing and Product Classification
Production Techniques
C/C composites are manufactured through:
-
Preform Layup: Carbon fibers are woven into 2D, 3D, or 4D architectures.
-
Matrix Densification:
-
Liquid Impregnation (LIP): Uses phenolic resins or pitch, carbonized to form a matrix.
-
Chemical Vapor Infiltration (CVI): Deposits pyrolytic carbon via hydrocarbon gases, ideal for high-density components.
-
-
Graphitization: Heat treatment up to 2700°C enhances crystallinity and thermal conductivity.
Product Categories
-
Structural Grades:
-
2D/2.5D Sheets: Used in furnace fixtures and insulation blankets (density: 1.4–1.6 g/cm³).
-
3D/4D rods and blocks: Optimized for high performance application, with densities up to 1.9 g/cm³.
-
-
High-Performance Grades:
-
CVI-Densified Composites: For rocket nozzles and thermal protection systems.
-
Silicon Carbide-Coated C/C: Enhances abrasion resistance in wind turbine blades.
-
4. Applications Across Industries
-
Aerospace: Leading edges of space shuttles (RCC panels) and solid rocket motor nozzles.
-
Automotive: Formula 1 brake disks (50% lighter than steel, 3x lifespan).
-
Energy: Heating elements for silicon crystal growth furnaces (thermal shock resistance).
5. Future Trends: Nano-Modified Composites
Emerging technologies focus on integrating carbon nanotubes (CNTs) and graphene into C/C matrices. These nanomaterials improve fracture toughness by 40% and reduce oxidation rates through tighter pore structures212. CFC Carbon’s R&D team is pioneering CNT-reinforced composites for hypersonic vehicle applications.
Why Choose CFC Carbon?
As a government-certified manufacturer with 45+ years of expertise, CFC Carbon delivers:
-
Custom Solutions: Tailored 2D–5D architectures and densities (1.4–1.9 g/cm³).
-
Cost-Effective Production: Batch processing reduces costs by 30% for industrial molds and insulation barrels49.
-
Global Compliance: Products meet MIL-STD and aerospace certification standards.
related news /articles:
Matrix inhibition / coating of CC composite material
Oxidation of inhibited carbon-carbon composite (2)
Applications of carbon-carbon composite (4)-High-Performance Industries
Mechanisms of protection of C-C composites against catalytic oxidation (2)