It follows from data in figs3 and 4 that the temperature range for high-temperature treatment from 1270°C to ~1500°C from carbon-carbon composites of the composition and structure indicated has a range of steady-state condition. A composite in this condition may have commercial value if its operating temperature does not exceed the upper level of this range. On the basis of data in Figs 1 and 2 proceeding from the calculated level of error, it is desirable to designate the production temperature for treatment from (1270+50) to (1500-50)°C.
The threshold of a change in weight loss curves, porosity, resumption of shrinkage, stabilization of specific electrical resistance, is completed in the temperature range △T≈200°C with a nominal average value of 1500°C. It is possible to confirm that 100°C lower and a 100°C higher than the nominal temperature is a qualitatively different state of carbon substance. Directive specifications predetermine temperature regime for a slow heating rate and introduction of isothermal exposure in industrial implementation of HTT.
The practice of manufacturing large thin-walled blanks of carbon composite has demonstrated the important value of HTT for retaining their geometric shape. As may be seen from fig.4, above 1500-1700°C there is a marked reduction in mechanical strength. A reduction might be expected in resistance to blank shape change and development of component distortion. As is well known, carbon materials in the initial stage of the next period of structural rebuilding have irreversible shape changes and comply with an external load.
A clear picture of composite instability in this temperature range is the change in specimen shape with
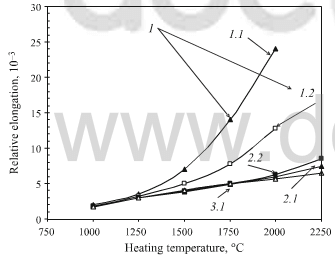
fig.5-shape change for carbon composite specimens during heat treatment
determination of a certain average LTEC by a dilatometric method during heating above a previously achieved production treatment temperature. Deformation curves of previously carbonized material are presented in fig.5. A composite was prepared on the basis of carbon cloth UT-900, which in turn was manufactured from carbon structural fibers grade UKM of polyacrylonitrlle, having a limiting production treatment temperature below 1600°C. Up to the heating temperature range [1250-(1500-50)]°C a composite may be considered thermally stable. On heating above 1500°C specimen elongation increases sharply. The limiting temperature for polymer heating is ~2000°C. Anisotropy of cloth textile structure and composite is reflected in anisotropy and shape change. With repeated heating to 2250°C the thermal shock resistance of a composite increases, and some shape change may only be seen above the primary heating temperature. In the third heating stage there is shape change, and in all temperature ranges a constant LTEC is established, not depending in this case on the measurement direction. Structure formation processes have been completed.
Irreversible specimen material shape changes may lead to irreversible changes in shape and component distortion.
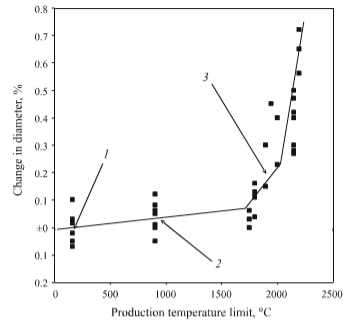
fig.6-change in blank diameter during production operations
Shape changes are presented in fig.6 for a conical blank, whose manufacturing technology is given in [6], for its least diameter during manufacture. The change in blank diameter was calculated in percentage as the ratio of the difference in greatest and least diameters in cross section to the average size with a wall thickness of 10-12 mm and a nominal blank diameter in the measurement zone of ~2250 mm. With these sizes blanks are referred to as thin-walled, i.e., the ratio of thickness to diameter is less than 0.01, and their stiffness is relatively low.