In order to clarify the mechanism of the process activation Arrhenius activation energy was evaluated. The molecular rebuilding of a carbon substance should show an activation energy commensurate with the energy of the C-C bond. Diffusion processes have activation energy an order of magnitude less. In this case evaluation of activation energy of the change in material specific electrical conductivity in the treatment range from 600 to 1500°C gives a value close to (38±2) kJ/mole. Previously a similar order of the value of activation energy was found for the dependence of the change in amount of material, shrinkage through a spcimen thickness during carbonization. For the dependence of the change in shrinkage rate for carbon material during carbonization in the period of most intense chemical transformations the level of activation energy found is ~20kJ/mole. For the test carbonized material shrinkage was studied separately through the thickness of a specimen in the temperature range after completion of the main chemical transformations during 960 sec, until geometric dimension relaxation was complete. Here the level of activation energy found was 12.0 kJ/mole. These levels, markedly less than that for the level of chemical bond energy in carbon materials, indicating a relatively weak connection of the level of the degree of transformation with temperature, correspond to the kinetics of diffusion, and volumetric relaxation processes in a solid. The difference in levels from 12 to 38 kJ/mole may be connected with a change in plastic deformation resistance of the carbon matrix at the start and completion of carbonization. Thus, with a temperature up to 1200°C in forming the level of specific electrical resistance there is predominance of compaction of the carbon material due to shrinkage. Shrinkage in turn, due to a difference in deformation properties of the matrix and filler, generates internal stresses at a microlevel. The relative sl down in reduction of specific electrical conductivity to the range 1300-1400°C and its almost unchanged nature about up to 1400°C point to completion of the individual stage of carbon matrix structure formation.
Starting with a treatment temperature of about 1500°C (see fig.3) there is a resumption of an increase in open porosity. An increase in porosity follows a resumption in weight loss, and also coincides with intensification of shrinkage, which is reflected in material compaction. It may be seen from te dependences presented with a change in open porosity, weight loss, and shrinkage, that the absolute intensity of physicochemical processes during carobnization markedly exceeds the rate of change in the stage of polymer binder hardening and up to the start of its thermal destruction.
In practice, in performing HTT at about from 1560 to 1680°C in electric vacuum furnaces in this temperature range in some cases an increase is recorded in absolute pressure from 3.6 to 90 kPa. Here in the working production regimes there is a reduction in heating in order to provide the capacity of vacuum pumps to restore the original absolute pressure. Only then is heating resumed for the product being treated. On the whole however, weight loss in this temperature range is relatively small, and corresponds to 4.0-4.7%. This abount is less by almost a factor of five than weight loss during the preceding carbonization.
Strength in bending test results are shown in Fig.4 for specimens in relation to temperature. At 1300-1400°C the
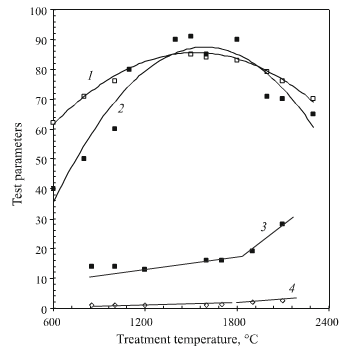
fig.4-ultimate strength in bending of carbon materials
relatively greatest level of strength of carbonizaed material is established. Experimental results have a maximum at 1400°C. Strength exceeds by almost a factor of two that of material in the stage of carbon coke formation from pyrolyzed binder. The relative increase in mechanical strength of a carbon composite may be a consequence of matrix shrinkage and compaction noted above. At 1300°C, as is well known, apparent and true density of “glassy carbon” are at a maximum, i.e., industrial carbon material represented by phenol formaldehyde resin coke.