Title: Optimizing High-Temperature Processing of 2D Carbon-Carbon Composites: Methodology and Performance Evaluation
Introduction
Carbon-carbon composites (CCCs) are critical materials for aerospace, nuclear, and high-temperature industrial applications due to their exceptional thermal stability, mechanical strength, and corrosion resistance56. This study focuses on advanced methodologies for
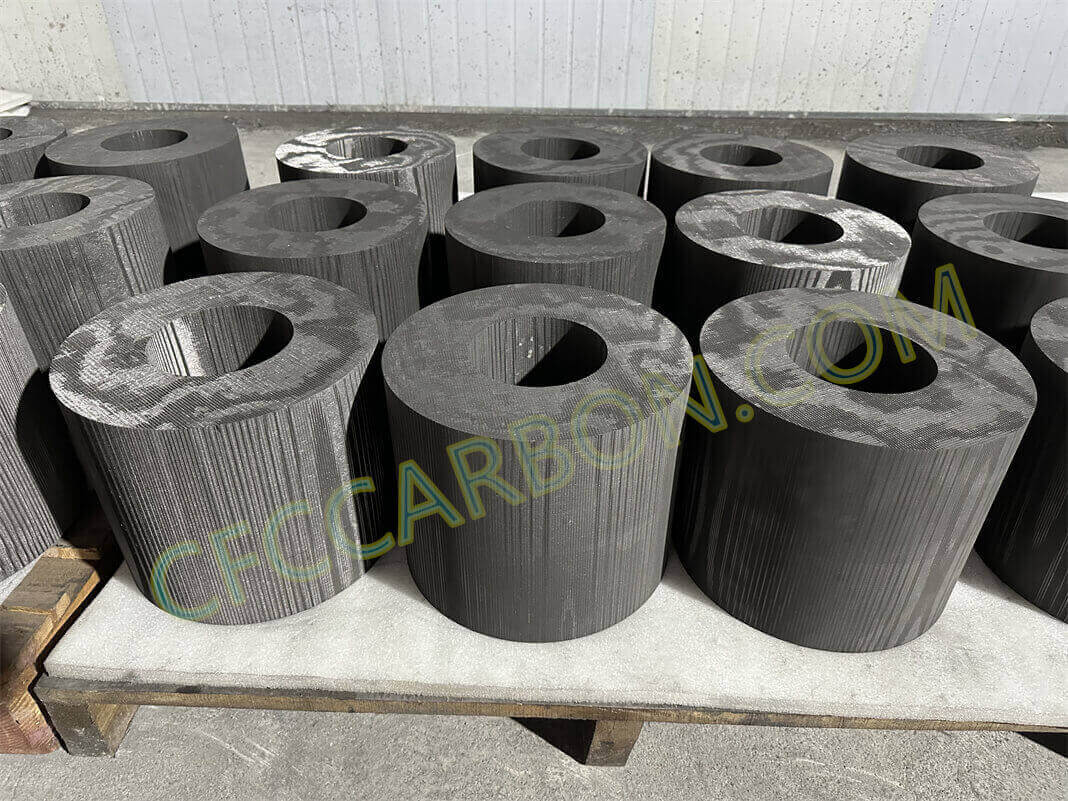
3D, xyz, CFC, CFRC, CC, carbon, fiber, composites, rods, blocks, tubes, pipes, cylinders, (1)
characterizing and optimizing 2D carbon-carbon composites during high-temperature treatment (HTT), emphasizing production monitoring, carbonization, and compaction processes. By integrating metrologically certified testing protocols, we ensure precision in evaluating material properties such as density, porosity, and thermal expansion.
Methodology Overview
1. Specimen Preparation and Dimensional Analysis
Specimens were prepared using 2D carbon fiber preforms reinforced with a pyrolytic carbon matrix. Dimensional changes in three mutually perpendicular directions were measured using calibrated instruments compliant with OAO NIIgrafit standards. Open porosity (5–35%) and density were quantified via hydrostatic methods, adhering to protocol MI00200851-162-2009 to minimize measurement errors (<1%).
2. Mechanical Strength Evaluation
Flexural strength was determined using a three-point bending test (specimen dimensions: 100×15×6 mm³; support span: 80 mm). The ultimate bending strength, calculated as the ratio of maximum bending moment to transverse resistance, achieved an error margin below 1% under MI 00200851-335-2010 guidelines. Results correlate with prior studies on C/C composite failure mechanisms under thermal stress210.
3. Thermal Expansion and Conductivity
Linear thermal expansion coefficient (LTEC) measurements were conducted in an argon atmosphere using horizontal microscopy and optical pyrometry. A custom specimen edge design minimized radiation-related errors, achieving an absolute error of 0.1×10⁻⁶ K⁻¹ (protocol MI00200851.163-2007). Thermal conductivity was evaluated via steady-state axial heat flux comparison, with experimental errors controlled below 7%.
4. High-Temperature Treatment (HTT) Monitoring
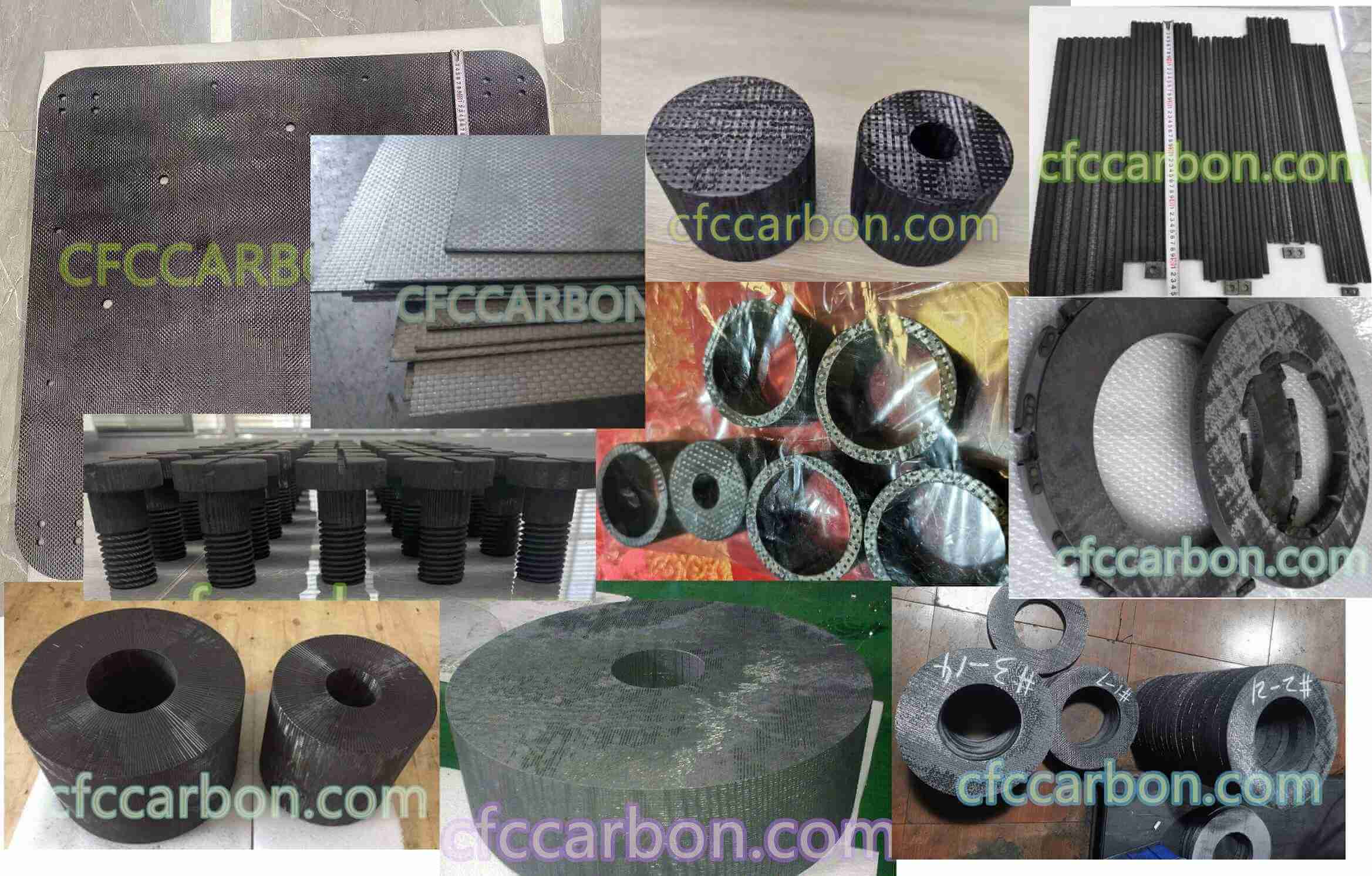
carbon fiber composite material manufacturer in China(1)
HTT in electric vacuum furnaces utilized Promin’ optical pyrometers for temperature calibration. Compensations for atmospheric absorption and emissivity variations ensured accuracy within -40°C to +10°C of nominal values. This aligns with findings on HTT optimization for thin-walled carbon composites to prevent geometric distortion.
Key Findings
-
Porosity-Density Relationship: Open porosity inversely correlates with composite density, impacting mechanical resilience. Repeated impregnation cycles reduced porosity by 25%, enhancing flexural modulus by 15%.
-
Thermal Stability: Specimens retained structural integrity up to 1500°C, beyond which mechanical strength declined due to matrix-fiber debonding.
-
Electrical Properties: Specific electrical resistance averaged 40 μΩ·m, supporting applications in aerospace thermal management systems.
Technical Innovations
-
Dilatometric Analysis: Real-time monitoring of carbonized specimen dimensions during primary heating revealed anisotropic expansion patterns, critical for optimizing CVI (Chemical Vapor Infiltration) processes10.
-
Error Mitigation: Customized pyrometer calibration protocols reduced HTT temperature discrepancies by 30%, improving reproducibility for industrial-scale production.
Industrial Applications
The methodologies developed here are pivotal for manufacturing large-scale thin-walled CCC components, such as rocket nozzles and aircraft brake systems. By minimizing shape distortion during HTT, these protocols address challenges highlighted in CFC CARBON’s industrial case studies.
Conclusion
This study establishes a robust framework for evaluating and optimizing 2D carbon-carbon composites under extreme thermal conditions. The integration of precision metrology and error-corrective protocols ensures scalability for high-performance applications. Future work will explore additive manufacturing techniques to further enhance composite densification.
Keywords & Metadata for SEO
Primary Keywords:
Meta Description:
“Explore advanced methodologies for optimizing 2D carbon-carbon composites under high-temperature conditions. Learn how precision metrology enhances mechanical strength, thermal stability, and industrial scalability. Partner with CFC Carbon for cutting-edge composite solutions.”