The properties of carbon-carbon composites are discussed by Savage and Chung and by Huttner. Carbon-carbon composites are much stronger than graphite components and properties are improved further with a three dimensional construction. Peters et al determined the strength of unidirectional carbon fiber reinforced carbon matrix composites with fiber treated at different oxidation levels, after each step of the production cycle. An impregnated bundle had a strength 1.9-4.3 time the strength of a loose bundle, but after carbonization, the strength was less than that of a loose bundle. This was attributed to the formation of defects in the fiber due to shrinkage during carbonization. The defects were larger with a good fiber/matrix bond in the green material. Low strength of the composite was not caused by stress concentration effects.
Flexural strength and modulus of carbon-carbon increase with the density, the strength increasing up to a value of about 500 Mpa. The flexural modulus has a value about twice that of resin matrix composites.
Sato and co-workers prepared three types (A, B, C) of carbon-carbon composites and found that all composites had superior mechanical properties to a control sample of isostatically pressed fine grained graphite. The PAN based C/C composite (B) was superior to the other composites (A and C) despite having a lower fiber content, C except the rayon based composite (C) did have superior tensile strength. The low thermal shock resistance of the rayon based composite was attributed to interlaminar failure between the plies of woven reinforcement, whereas the felt composites (A and B) had higher values, possibly attributed to the adventitious effect of partial 3D strength imparted by the felts.
Typical properties of carbon-carbon composite are given in Table bellow, its 3D C/C composite.
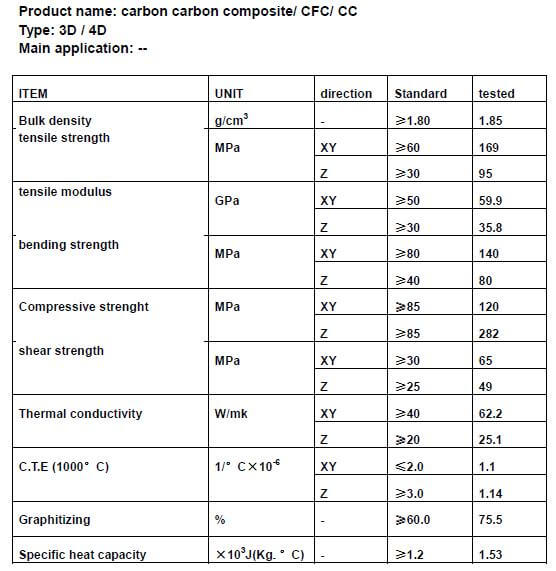
3D carbon-carbon composite properties
The mechanical properties are significantly affected by the heat treatment temperature and the level of surface treatment. Manocha et al. showed that a carbon-carbon composite when carbonized at 1000C will exhibit significant differences when graphitized at 2700C. There is a 54% in creak in flexural strength, 40% decrease in ILSS and a 932 increase in flexural modulus. These results are strongly indicative of a change in the fiber matrix interaction. The increase in modulus can be probably attributed to the further graphitization of the pitch based fiber assisted by envelopment within the carbon matrix. Huttner states that the toughness peaks at a level of about 2400C and values for thermal and electrical conductivities are given in Table 20.31.
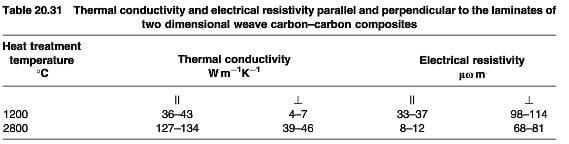
thermal conductivity and electrical resistivity parallel change of 2D CC composite
The thermal conductivity of vgcf has a particularly high value of about 1900 W/m.K at 25C and when incorporated in a carbon matrix can produce a composite with a thermal conductivity >1000 W/m.K.