The C-C facesheet tested was one of the 9 identical facesheets fabricated by BFGoodrich under a Navy contract. The facesheet was constructed as a 30-inch square panel using 2-ply fabric made with 2K-tow, P30 fiber. The fabric was laid up to provide quasi-isotropic reinforcement. Due to issues involving the width of the fabric it was necessary to offset the principle fiber directions 22.5° from the edges of the panels. The panel was prepregged using Hi-K process and densified using chemical vapor infiltration (CVI) carbon. The as-processed panel is shown in figure 4. The C-C facesheet material was evaluated for thermal conductivity, tensile strength and modulus, compression strength and modulus, interlaminar shear strength, interlaminar tensile strength, in-plane shear strength, bearing strength, and in-plane thermal expansion. BFGoorich cut the facesheet into smaller sub-panels, designated A through F, which were shipped to NASA Langley. Sub-panels D and E were cut in half lengthwise at Langley and glued together to achieve a double thickness sheet. The long direction of each panel was designated the 0° direction.
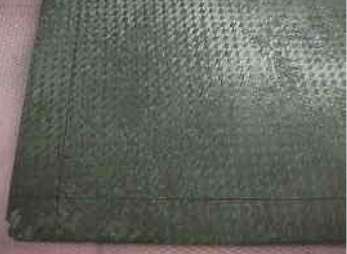
Fig.4-carbon-carbon composite facesheet prior to trimming
Thermal conductivity testing.
Thermal conductivity test specimens were cut from sub-panel A. six 0.25- by 6.0- by 0.22-inch specimens were cut in both the 0° and 90° directions. One half the specimens were sent to Lockheed Martin Astronautics and forwarded to TPRL and one half to NASA GSFC for testing.
The samples submitted to TPRL were tested using the Kohlrausch method. The Kohlrausch method involves the determination of the product of the thermal conductivity “λ” and the electrical resistivity “ρ”. Since the electrical resistivity is measured at the same time as the product of the resistivity and conductivity, λ can be calculated. The method involves passing constant direct current through the specimen to heat the sample while the ends are kept at constant temperature. Radial heat losses are minimized by an external heater whose center temperatures are maintained at the sample’s midpoint temperatures and whose ends are also cooled by water or liquid nitrogen. Thermal conductivity values accurate to within ±5% are obtained by the Kohlrausch method and all measured quantities are directly traceable to NIST standards.
TPRL tested two of the six specimens. The results for sample TC-5 are given in Table Ⅰand the result for sample TC-11 are listed in Table Ⅱ.
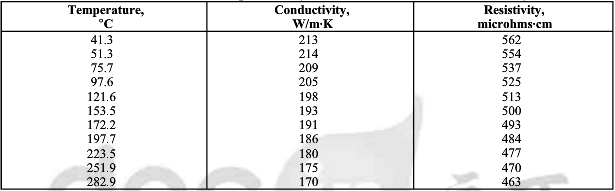
Table 1
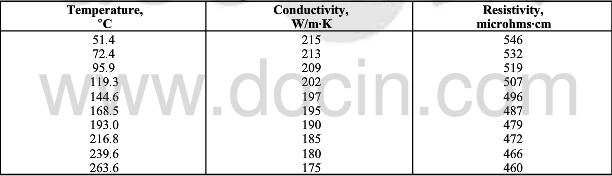
table 2
The samples submitted to GSFC were used to measure the thermal diffusivity and specific heat of the composite facesheet. The thermal conductivity was calculated from thermal diffusivity (γ), specific heat (Cp), and density (d) using the following equation:
K=γ•Cp•d
Thermal diffusivity was measured using the Angstrom’s temperature wave method. The thermal diffusivity of 2 specimens was measured in the 0°-ply direction and in the 90°-ply direction for the others. The measured values from the 4 specimens did not vary much and were compiled together. Thermal diffusivity measurements were only possible up to about +40°C for these specimens. The specific heat was measured using a TA Instruments DSC 910 Differential Scanning Calorimeter. The density of this material was measured to be 1.78 ±0.01g/cm3. Table 3 is a summary of the thermal diffusivity measurements and conductivity calculations from 4 carbon-carbon composite specimens.
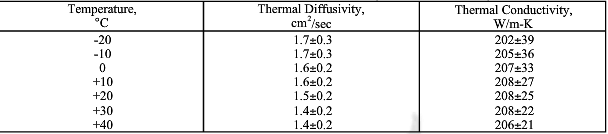
table3