The data presented in this paper allows one to determine the benefit of carbon-based ion optics systems over conventional ion optics fabricatd from molybdenum. To do this rigorously, the differential sputter yield data obtained in this program would need to be incorporated into a numerical model of an ion optics system that was able to calculated charge exchange ion generation rates and determine charge exchange ion trajectories and their subsequent energy and incidence angle as they strike the accel grid surface. However, the relative benefit of carbon over molybdenum can be estimated to first order by comparing the recession rates of surfaces being subjected to ion bombardment at normal incidence only. The rate of recession of a surface under normal incidence ion bombardment can be expressed as
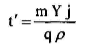
Eq.(10).
In Eq.(10), m represents the mass of a target atom, Y the total sputter yield, j the current density of bombarding ions, and ρ the density of the target.
The ratio of the recession rate of carbon to molybdenum is
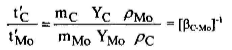
Eq.(11).
In Eq.(11) the subscripts C and Mo represent carbon (or graphite) and molybdenum and the parameter β represents the propellant throughput performance relative to molybdenum. The first order, a grid set constructed of carbon that is subjected to normal incidence ion bombardment would have β times more propellant throughput capability compared to molybdenum. Plots of β for carbon, porolytic graphite, carbon carbon composites, and titanium are shown in Fig.26. For xenon ion energies between 300 eV and 1000 eV, grids fabricated from graphite would be expected to last 5 to 6.5 times longer than moly grids, and PG or CC grids would last 8 to 9.5 times longer. The curve for titanium grids shown in Fig.26 suggests that this material would only be equivalent or slightly better than molybdenum in terms of propellant throughput over the entire 200 eV to 1000 eV range shown. It is noted that significant improvements in propellant throughput would be expected for carbon-based ion optics systems if the bombarding ion energy could be held to 250 eV and lower.
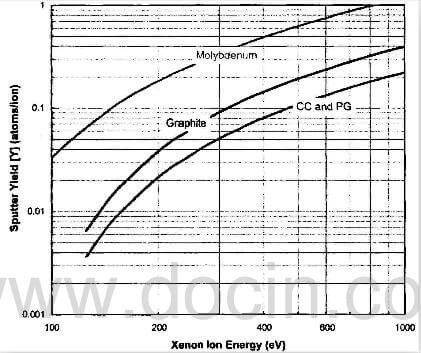
fig.26-comparison-of-molybdenum-graphite-and-CC-PG-sputter-yields-at-normal-incidence.
Differential and total sputter yield measurements were presented for xenon ion bombardment of pyrolytic graphite (PG) and carbon-carbon composite (CC) materials. Both the ion energy and incidence angle were varied during this study over ranges from 200 eV to 1000 eV and normal incidence (0°) to 60°. Data collected at an incident angel of 5° showed that differential sputter yields for pyrolytic graphite are extremely sensitive to incident angle and great care has been taken to align the ion beam and target normal directions. A high perveance grid assembly with small screen and accel grid holes and small screen grid-to-accel grid spacing was manufactured to enable testing at xenon ion energies of 200 and 300 eV. An important finding in this study was that the carbon-carbon composite sample displayed differential and total sputtering yield behavior that was nearly identical to the pyrolytic graphite sample. This result implies that the PVD infiltrated and pyro-coated carbon-carbon composite material should behave in a way that is similar to pyrolytic graphite in terms of erosion due to xenon ion bomdardment. Furthermore, the total sputter yields of pyrolytic graphite and carbon-carbon composite at normal incidence were 40% less than values measured for electronic grade graphite. Temporal experiments were completed in which the pyrolytic graphite and carbon-carbon composite samples were subjected to the same sputtering conditions over many hours while periodic measuremets were made of the differnetial sputter yield profile. Very little change in the differential sputter yield profile was detected over tesing periods of 30 hours for eigher sample. This result suggests that the sputtering characteristics of the samples provided do not change considerably under ion bombardment even though tens of microns of material were removed during testing.