Introduction to Carbon-Carbon Composites
Carbon-carbon (C/C) composites are advanced materials consisting of carbon fibers reinforced with a carbon matrix. Known for their exceptional thermal stability, high strength-to-weight ratio, and resistance to extreme environments, these composites are widely used in aerospace, automotive, and industrial applications. With a density of 1.80 g/cm³, this particular grade of C/C composite offers a balanced combination of lightweight properties and structural integrity, making it ideal for high-performance applications.
Key Properties of 1.80 g/cm³ Carbon-Carbon Composite
The 1.80 g/cm³ density variant provides an optimal blend of mechanical strength and thermal conductivity. Compared to higher-density composites (e.g., 1.85 g/cm³, as seen in CFC Carbon’s product lineup), this material maintains excellent rigidity while reducing weight—critical for aerospace components like brake discs and rocket nozzles. Its tensile strength ranges between 200–300 MPa, ensuring durability under stress.
Data sheet of 1.80 g/cm³ Carbon-Carbon Composite:
ITEM | UNIT | direction | Standard | Tested |
Bulk density | g/cm3 | – | ≥1.80 | 1.825 |
tensile strength | MPa | XY | ≥120 | ≥140 |
Z | ≥60 | ≥100 | ||
tensile modulus | GPa | XY | ≥35 | ≥36 |
Z | ≥25 | ≥30 | ||
bending strength | MPa | XY | ≥80 | ≥130 |
Z | ≥50 | ≥70 | ||
Compressive strength | MPa | XY | ≥90 | ≥100 |
Z | ≥150 | ≥200 | ||
shear strength | MPa | XY | ≥30 | ≥45 |
Z | ≥20 | ≥28 | ||
Thermal conductivity | W/mk | XY | ≥40 | ≥40 |
Z | ≥20 | ≥25 | ||
C.T.E (1000°C) | 1/°C×10-6 | XY | ≤2.0 | ≤1.5 |
Z | ≤3.0 | ≤2.0 | ||
Graphitizing | % | – | ≥55 | ≥60 |
Plasma line ablation rate | mm /s | ≤0.15 | ≤0.13 | |
Specific heat capacity | ×103J(Kg.°C) | – | ≥1.1 | ≥1.2 |
Surface requirement | The product shall not have cracks, holes, delamination, etc. visible to the naked eye. However, due to its low density, there are pores and looseness, which increase the contact area with oxygen during the ablation process, resulting in accelerated ablation. | |||
X-ray test | No significant defects or porosity, No longitudinal shadow stripes are allowed, the total number of circumferential shadow stripes shall not exceed 10, and the stripe spacing shall not be less than 5mm. However, due to its low density, it is difficult to distinguish whether it is a crack or insufficient density during X-ray inspection. |
Thermal and Electrical Conductivity
Thanks to its all-carbon structure, this composite exhibits superior thermal conductivity (80–120 W/m·K) and electrical conductivity, making it suitable for high-temperature environments such as furnace fixtures and semiconductor manufacturing. The slightly lower density compared to 1.85 g/cm³ grades may result in marginally reduced thermal resistance but enhances versatility for weight-sensitive designs.
Comparison with 1.85 g/cm³ Variants
Referencing CFC Carbon’s 1.85 g/cm³ C/C composites, the 1.80 g/cm³ version trades a small fraction of thermal stability for improved
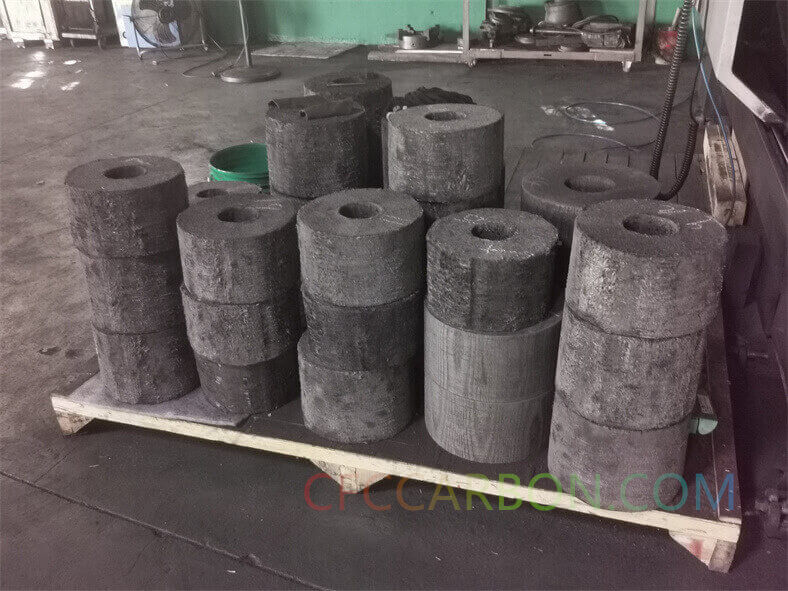
3D carbon fiber composite material manufacturer factory (1)
weight efficiency. For instance, while the 1.85 g/cm³ material excels in ultra-high-temperature applications (>2000°C), the 1.80 g/cm³ variant is preferable where weight savings are paramount, such as in satellite components or racing car brakes.
Price difference between 1.80 g/cm3 and 1.85 g/cm3 carbon-carbon composite: the price difference is about 15%, it means the 1.80g/cm3 type is about 15% lower in price than the 1.85g/cm3 type carbon composite. but to keep a stable application result, we strongly suggest you take the grade 1.85 g/cm3 type.
Manufacturing and Applications
Produced by resin impregnation, then carbonization, then graphitization in high temperature furnace, then in CVI (chemical vapor infiltration) process; this is a repeated processing cycle. the one complete process takes one month, that’s why the big size products take a long production time. this composite’s microstructure ensures uniform density and minimal voids. Industries leverage it for:
- Aerospace: Re-entry shields, propulsion systems.
- Energy: Heat exchangers, nuclear reactor components.
- Automotive: Lightweight brake systems.
Conclusion
The 1.80 g/cm³ carbon-carbon composite strikes a critical balance between performance and efficiency. While alternatives like 1.85 g/cm³ (see CFC Carbon) offer marginal gains in thermal properties, this grade remains a top choice for applications demanding both strength and weight optimization. For detailed specifications, visit manufacturers’ data sheets or technical portals.
related news /articles:
Prices of 3D carbon carbon composite | C/C composite material
Data sheet of 3D carbon carbon composite | C/C composite material
Properties of high density carbon carbon composite | C/C composite