1. What Are Carbon-Carbon Composites and Their Coating Systems?
Carbon-carbon (C/C) composites are advanced materials composed of carbon fibers embedded in a carbon matrix. Renowned for their
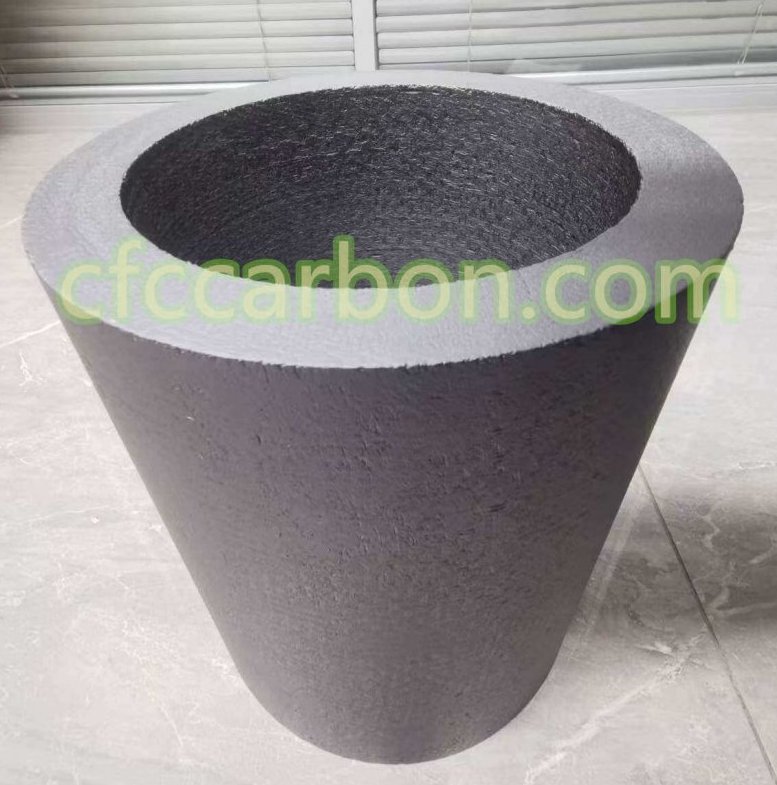
SiC coating carbon fiber composite material-CC-CFC (2)
exceptional high-temperature stability (up to 2,000°C in inert environments), lightweight nature, and superior mechanical strength, these composites are widely used in aerospace, brake systems, and industrial heating applications25. However, their Achilles’ heel is oxidation vulnerability above 400°C in oxygen-rich environments. To address this, coating systems are applied to shield C/C composites from oxidation, thermal shock, and wear. These coatings often involve chemical vapor deposition (CVD) of ceramics like silicon carbide (SiC) or silicon nitride (Si₃N₄), combined with graded layers and sealants to enhance durability.
2. Production, Classification, Applications, and Performance
A. Production and Manufacturing Innovations
C/C composites are manufactured through two primary methods:
-
Chemical Vapor Infiltration (CVI): Hydrocarbon gases like methane decompose at high temperatures, depositing pyrolytic carbon onto carbon fiber preforms.
-
Liquid Impregnation: Carbon fibers are soaked in pitch or resin precursors, followed by carbonization and graphitization cycles to densify the matrix.
Advanced techniques like plasma-assisted CVD reduce cracking by lowering deposition temperatures, while graded coatings (e.g., SiC-to-carbon gradients) mitigate thermal expansion mismatches.
B. Product Classification
C/C composites are categorized by fiber architecture:
-
2D/2.5D: Ideal for aircraft brake discs and heating elements due to balanced strength and cost-effectiveness.
-
3D/4D: Used in rocket nozzles and thermal protection systems for multidirectional load-bearing capabilities.
-
High-Density (1.9 g/cm³): Enhanced thermal conductivity for aerospace components, produced via CVI or pitch-based processes.
C. Key Applications
-
Aerospace: Leading edges of spacecraft, rocket nozzles, and re-entry heat shields.
-
Automotive: Formula One brake discs and high-performance vehicle components.
-
Industrial: Heating elements, furnace fixtures, and thermal insulation barrels.
D. Performance Characteristics
-
Thermal Stability: Retains strength above 2,000°C in non-oxidizing environments.
-
Low Thermal Expansion: Minimizes structural deformation under thermal stress.
-
Oxidation Resistance: Achieved via coatings like SiC or iridium for extreme temperatures (>1,800°C).
3. Coating Systems for Enhanced Durability
A. Low-Temperature Regime (<1,400°C)
SiC and Si₃N₄ coatings dominate this range but face cracking due to thermal expansion mismatches. Solutions include:
-
Glass Sealants: Tetraethyl orthosilicate (TEOS)-derived silica fills cracks, while borate glasses (modified with SiO₂) reduce moisture sensitivity.
-
Internal Sealants: Borate additives within the composite expand upon oxidation, sealing microcracks.
B. Intermediate-Temperature Regime (1,400–1,800°C)
SiO₂-based coatings are critical but face devitrification and carbon reduction issues. Innovations focus on:
-
Hybrid Layers: Combining SiC with refractory metals (e.g., hafnium diboride) to slow oxidation.
-
Plasma-Sprayed Coatings: Improve adhesion and reduce porosity for thermal cycling resilience.
C. High-Temperature Regime (>1,800°C)
Iridium coatings excel here, offering oxygen impermeability and stability up to 2,110°C. Challenges include volatility and cost, prompting research into oxide-ceramic blends (e.g., ZrO₂-HfO₂).
4. Industry Leader Spotlight: CFCCARBON’s Innovations
CFCCARBON LTD (www.cfccarbon.com) exemplifies advancements in C/C composite technology:
-
Customizable Solutions: 2D, 3D, and 4D architectures tailored for aerospace brakes, insulation barrels, and heating elements.
-
High-Density Composites: Up to 1.9 g/cm³ for demanding applications like rocket motor nozzles.
-
Coating Integration: SiC and CVD coatings enhance oxidation resistance, extending product lifespans.
5. Future Trends and Challenges
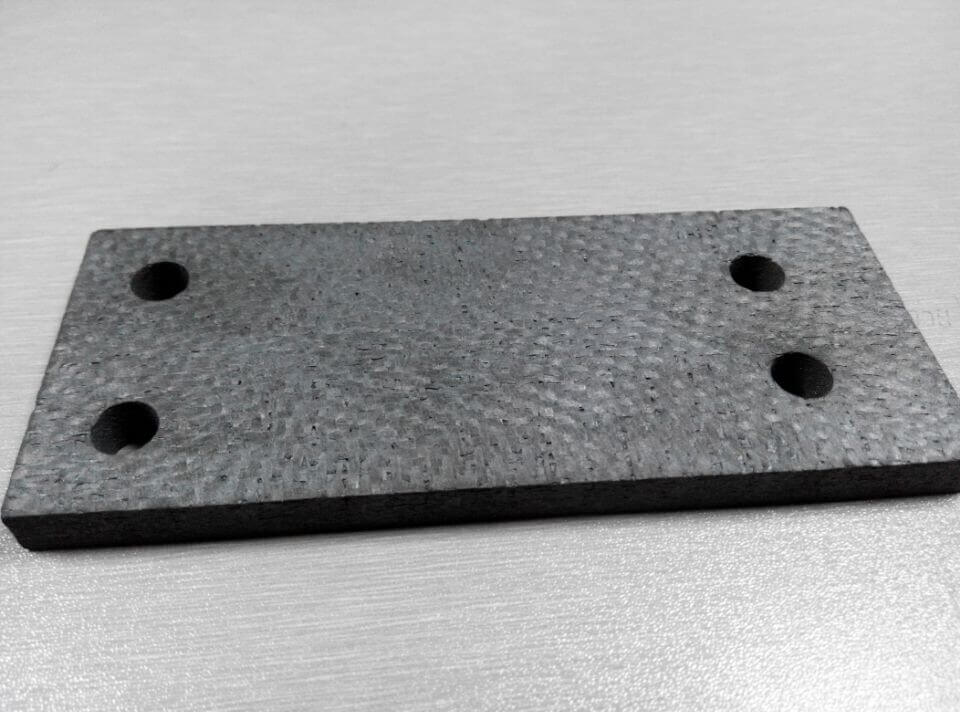
C-SIC
-
Self-Healing Coatings: Materials that autonomously repair cracks during operation.
-
Nanocomposites: Carbon nanotube (CNT)-reinforced interfaces for improved fracture resistance.
-
Cost Reduction: Scaling production via automated CVI and hybrid manufacturing.
Revolutionizing High-Temperature Materials: Advanced Coating Systems for Carbon-Carbon Composites
May 18, 2025 — Carbon-carbon (C/C) composites, the backbone of aerospace and industrial high-temperature applications, are undergoing a transformative leap with next-generation coating technologies. Companies like CFCCARBON LTD (www.cfccarbon.com) are at the forefront, delivering innovative solutions to overcome oxidation and thermal cycling challenges.
Breaking Down Coating Innovations
-
SiC and Si₃N₄ CVD Coatings: CFCCARBON utilizes plasma-assisted CVD to deposit crack-resistant silicon carbide layers at reduced temperatures, enhancing adhesion for aircraft brake discs and rocket components.
-
Iridium for Extreme Environments: Withstanding temperatures exceeding 2,000°C, iridium-coated C/C composites are revolutionizing spacecraft heat shields, though research continues to address cost barriers.
-
Graded and Hybrid Systems: Multilayer coatings (e.g., SiC-ZrO₂) mitigate thermal expansion mismatches, critical for reusable launch vehicles.
Applications Driving Demand
-
Aerospace: NASA-tested coatings now enable 10–20-hour mission durability in simulated re-entry conditions.
-
Automotive: Formula One teams leverage CFCCARBON’s 3D C/C brake discs for unmatched thermal stability.
-
Energy: High-density C/C heating elements (1.9 g/cm³) optimize furnace efficiency in semiconductor manufacturing.
Sustainability and Cost-Efficiency
CFCCARBON’s R&D focuses on scalable production, integrating AI-driven CVI processes to reduce costs by 30% while maintaining ISO-certified quality. Their latest 2.5D composites offer a 50% longer lifespan than traditional graphite fixtures, reducing industrial waste.
Looking Ahead
With patents pending in self-healing nanocoatings and CNT-enhanced interfaces, the future of C/C composites promises unprecedented reliability. As CFCCARBON’s CTO notes, “Our goal is to make oxidation-resistant C/C composites accessible across industries, from wind turbines to next-gen hypersonic vehicles.”
For custom C/C solutions, visit www.cfccarbon.com or contact sales@cfccarbon.com.
related news /articles:
Understanding Oxidation Mechanisms in Carbon-Carbon Composites
Introduction of high-temperature coatings on CC composite material
Overcoming the Oxidation of carbon carbon composite and coatings on CC composite
Advanced Protective Coatings for Carbon-Carbon Composites