The USA is the predominant user of carbon-carbon components, with some 80% of the market split more or less equally between aircraft brakes, re-entry vehicles and rocket nozzles.
Carbon-carbon braking systems: Over 60% of carbon-carbon manufactured is used for braking systems in airplanes, high speed trains, racing cars, motorcycles and tanks.
Aircraft brakes are made up of multiple disks of carbon-carbon, comprising rotors attached to the wheel and stators attached to the brake assembly. The braking action is achieved by hydraulically pressing the disks together. Stimson and Fisher have described the design and engineering of carbon brakes. Typical properties of a carbon-carbon composite are compared with steel in Table 23.12 and with high strength graphite in table 23.13. The carbon-carbon brakes offer a 40% weight saving over steel and their heat capacity is some two and a half times greater. A typical brake temperature of an aircraft on landing could be 500C, but in an emergency abandoned take-off, the temperature could reach 1300C, which would be quickly absorbed by the carbon-carbon acting as a heat sink. The thermal loading of a disk is severe and the frictional forces on the brake disk cause it to deflect radially up to some 3.5% of the diameter. In operation, the brake disks contact at local points only, forming an annulus of contact as the disk rotates and wear occurs, releasing carbon-carbon. The band then moves to a new position.
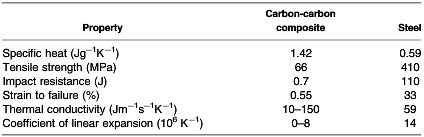
table.23.12-typical properties of brake disk material-carbon-carbon vs steel
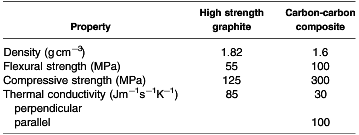
table.23.13-properties of high strength graphite compared with carbon-carbon composite
ABSC began testing carbon brakes in the laboratory leading to the first installation, in 1972, of a carbon brake on an F-15A aircraft. ABSC originally purchased their carbon-carbon from HITCO, but now produce all their requirements in-house, which is believed to be from a pitch based carbon fiber.
In 1972, BFG, at their Super-Temp Division in Santa Fe Springs, were the first company to develop the carbon-carbon brake and they can now handle carbon-carbon components up to 2.44 m in diameter and 3.66 m in length, providing heat treatment up to 2760C. Carbon/phenolic preforms are manufactured at the Aerostructure Group at Riverside, whilst carbonization and densification are undertaken at the Carbon Products Division at Pueblo. Since BFG use the CVD process to manufacture their brakes, they are albe to refurbish worn disks using the CVD densification process followed by re-machining, thereby doubling the life of the disk.
The SuperTemp process was licensed to Dunlop, who was the first to introduce carbon-carbon brakes into regular airline service, fitting the VC10 in 1973 and the Concorde in 1974. The physical and mechanical properties of a range of Dunlop carbon-carbon composites are given in table 23.14.
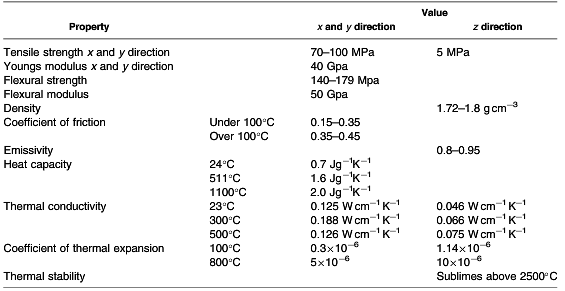
table.23.14-typical properties of carbon-carbon material for brake rotors, pads, clutch plates