The USA is the predominant user of carbon-carbon components, with some 80% of the market split more or less equally between aircraft brakes, re-entry vehicles and rocket nozzles.
A reader requiring detailed information on carbon-carbon materials and composites is referred to the following contents and the information given here is to provide an idea of the extensive range of end uses that have been developed for this product. Schmidt has described unique applications for carbon-carbon composite materials.
Application 1: carbon-carbon braking systems
Over 60% of carbon-carbon manufactured is used for braking systems in airplanes, high speed trains, racing cars, motorcycles and tanks. The principal brake manufacturers are CFCCARBON, SGL carbon group including HITCO. Each company has developed its own system of manufacture of carbon-carbon and the information is proprietary.
Aircraft brakes are made up of multiple disks of carbon-carbon, comprising rotors attached to the wheel and stators attached to the brake assembly. The braking action is achieved by hydraulically pressing disks together. Stimson and Fisher have described the design and engineering of carbon brakes and a section of the Concorde wheel. Typical properties of a carbon-carbon composite are compared with steel and with high strength graphite in table bellow. The carbon-carbon brakes offer a 40% weight saving over steel and their
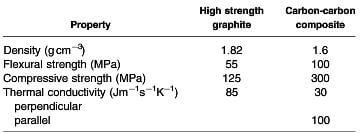
properties of high strength graphite compared with a carbon-carbon composite
heat capacity is some two and a half times greater. A typical brake temperature of an aircraft on landing could be 500C, but in an emergency abandoned take-off, the temperature could reach 1300C, which would be quickly absorbed by the carbon-carbon acting as a heat sink. The thermal loading of a disk is severe and the frictional forces on the brake disk cause it to deflect radially up to some 3.5% of the diameter. In operation, the brake disks contact at local points only, forming an annulus of contact
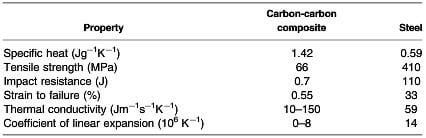
typical properties of brake disk material-carbon-carbon vs steel
at the disk rotates and wear occurs, releasing carbon-carbon. The band then moves to a new position.
ABSC began testing carbon brakes in the laboratory leading to the first installation, in 1972, of a carbon brake on an F-15A aircraft. ABSC originally purchased their carbon-carbon from HITCO, but now produce all their requirements in-house, which is believed to be from a pitch based carbon fiber.
The SuperTemp process was licensed to Dunlop, who was the first to introduce carbon-carbon brakes into regular airline service, fitting the VC10 in 1973 and the Concorde in 1974.
SEP first investigated carbon-carbon as a candidate for brakes in 1972 and became involved with aircraft brakes from 1978, whilst Carbone Industrie became involved from 1986. SEP was able to draw heavily on its own experience gained developing carbon-carbon for rocket propulsion, having produced commercial quantities of carbon-carbon from 1974 onwards. Carbon-carbon brakes were tested by Carbone Industrie on Formula One racing cars in 1997, enabling an F1 racing car to decelerate without fading from 350 to 100 km/h in three seconds, the mechanical characteristics improving as the temperature rose and lasting up to some six times longer than a conventional braking system. The braking performance of carbon-carbon at high speeds is exceptionally good and CI has developed brakes for France’s TGV trains, which operate in commercial service at speeds up to 350 km/h. It is likely, however, that carbon/SIC brake disks may offer improved performance in this application.
The friction, or efficiency factor (μ), of a brake varies during the braking process and initially, with a carbon-carbon brake, μ increases as the operating temperature rises, with fading occurring only at extreme temperatures, when other materials would have long since failed. For instance, each brake in an Airbus jetliner absorbs 70 MJ of energy, stopping the aircraft in 1,300 m with the peak temperature of the carbon-carbon rising to 2,300C.