Braided 3D multiaxial: Braiding is termed 3D when three or more systems of braiding yarns are involved to form a three-dimensional braid. Jacquard braiding uses a mechanism which facilitates connecting groups of yarns to braid different patterns simultaneously. Figure 21.42 shows a schematic view of 3D tape made by the braiding process.
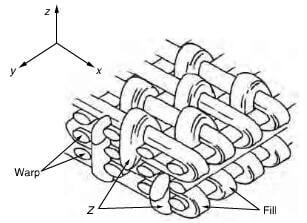
fig 21.42-schematic view of 3D tape made by braiding process.
n-D orthogonal blocks: A typical 3D block construction is shown in figure 21.43. Higher in-plane shear moduli can be achieved with 4D and 5D architectures. Using a polar 3D architecture provides axial tensile and compressive strengths in the Z-direction, whilst the hoop fibers provide hoop tensile strength and the radial fibers transmit radial compressive and torsional shear strength.
Hiroka et al have established that orthogonal woven composites have better compressive and flexural fatigue strengths than 2D composites.
Cahuzac divides the processes used by Aerospatiale for making 3D preforms into three categories:
- Processes using a network of rods- metallic wire rods set in thick pierced plates are used to simulate the longitudinal direction of the weave. The first process stage is on a weaving machine, when yarns are inserted between the rods in the Z direction accompanied by compaction/vibration to provide the correct bulk density. The second stage uses a special needle to push the rod out of the preform, but not cut of the plate. On its travels, the eye of the needle catches the correct yarn ends from the bottom of the lay-up and pulls them through to give a preform. It is possible to make orthogonal 3D blocks, polar 3D cylinders and cones and shapeable 3D cylinders. A numerical controller can be used to place the yarns between the rods.
- Fully computerized process using a mandrel. A foam mandrel with implanted metallic pins is the basis of the Novotex process.
- Weaving a thick fabric to produce a 2.5D fabric.
fig.21.456-typical 3D,4D,5D structure of CC block construction
An orthogonal 3D block can be made by a weaving machine fitted with two thick pierced stacked blocks holding a
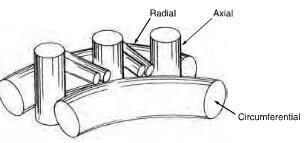
fig.21.46-3D cylindrical weave CC construction
series of rods in the Z direction. Two lateral rows of special needles situated under the top block interweave the X and Y yarns, which are compacted by pushing down after each layer. Once the requisite length of the fiber stack is achieved, it is removed from the weaving machine and positioned on a lacing machine, which is set to replace the rods with yarn to give the required preform.
Hearle and Du discuss the interaction of textile technology and composite engineering and Brookstein discusses braided and woven interlocked fiber architecture.