The advantage of the liquid precursor method for producing internal coatings is the direct application of the coating to areas that are most
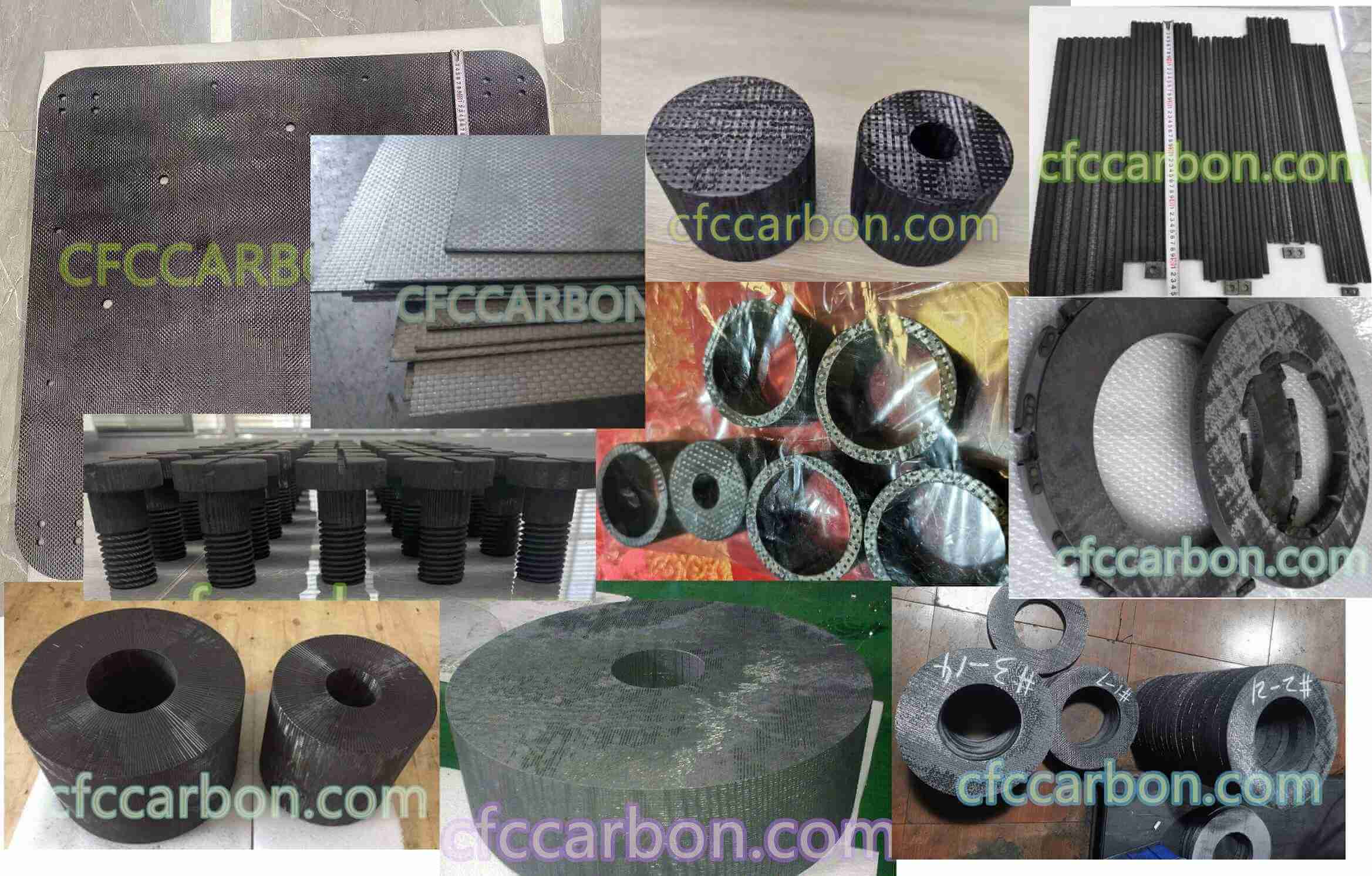
carbon fiber composite material manufacturer in China(1)
susceptible to oxidative attack. Disadvantages of this method include the need for muotiple processing cycles because of the low yield of most precursors, the need for compatibility between the carbon surfaces and liquid for thorough wetting to yield continuous and adherent coatings, and the need to control the high, potentially disruptive shrinkage that accompanies conversion of the liquid to a solid.
When used to incorporate glass formers, the matrix chemical modification technique has the advantage of producing increasing quantities of protective material as oxygen intrusion proceeds. This process results in the filling of surface pores and the formation of a coherent glass layer beneath the external coating. Particulate additions can be made simply and in relatively high concentrations. However, powders have the disadvantage of not penetrating the fiber yarn bundles and may mechanically damage fibers during composite consolidation. Segregation of the particulate between the fabric plies of CC composite laminates also increases the
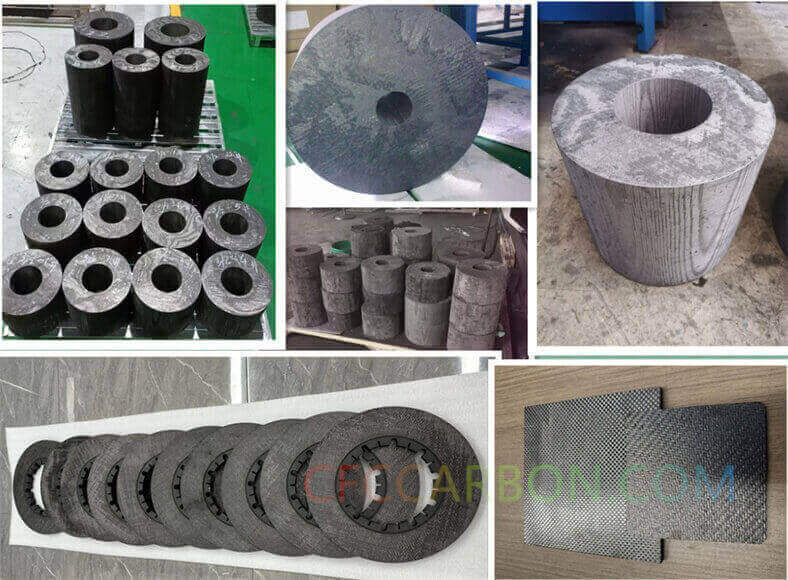
3D 4D carbon fiber composite material manufacturer factory -airplane brake disc plates sheets U L profiles-2D(s)
ply spacing and results in reduced inplane mechanical properties. These problems currently are being addressed by the use of fiber coatings and optimization of powder particle sizes.
Although molecular alterations to the resin or pitch matrix precursors have the advantage of penetrating the yarns to produce more uniform protection, the concentrations of active species that can be incorporated by this technique are much lower than can be achieved by powder loading. For this reason, the particulate loading and molecular alteration techniques may be most effective in combination with one another.
The CVI method for providing internal oxidation protection is extremely versatile; it can be used to chemically modify the carbon matrix, to coat the internal surfaces, or to completely replace the carbon matrix with another material. This method is limited to nonoxides when carbon is present and is a time-consuming and inefficient process as normally practiced when used to produce a composite matrix. However, recent work has demonstrated that satisfactory densification of fiber preforms can be accomplished in periods of 24 hours or less if the reactive gases are forced through the fibers and a thermal gradient is maintained to create a front of preferred deposition within the composite.
related news /articles:
3D C/C composite material manufacturer in China–CFCCARBON LTD
Characteristics of carbon carbon composite material
Wet-molded integral Rayon graphite felt insulation barrel-crystal growing furnace