Advanced Oxidation Protection Strategies for Carbon-Carbon Composites: Current Coating Technologies and Performance Limits
By CFCCARBON R&D Team | May 17, 2025
1. Understanding Carbon-Carbon Composites & Protective Coatings
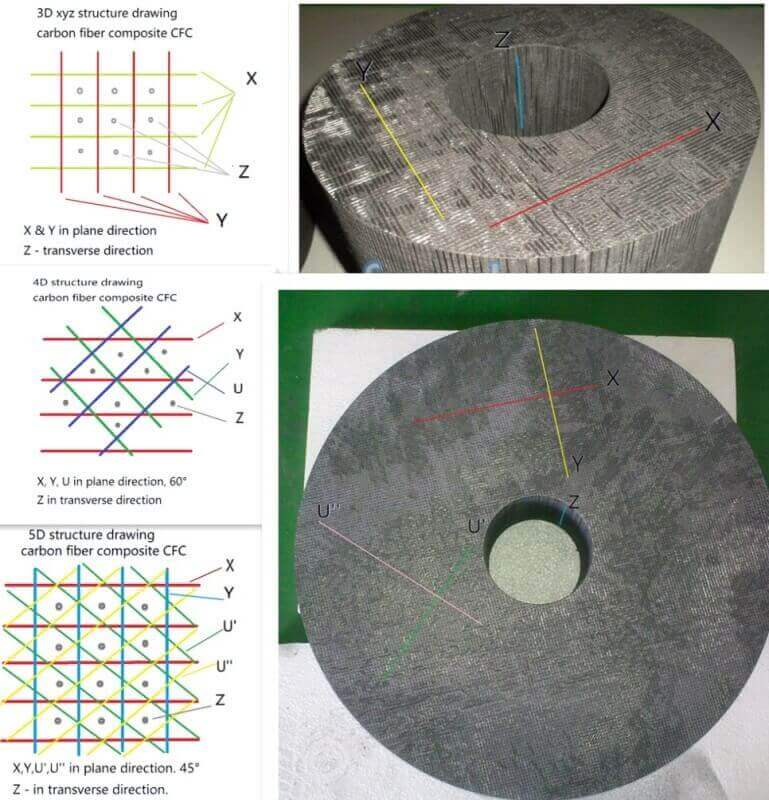
3D 4D 5D carbon fiber composite CFC structural diagram drawing material (1)
Carbon-carbon (C/C) composites are ultra-high-performance materials consisting of carbon fiber reinforcements embedded in a carbon matrix. These materials exhibit exceptional thermal stability (retaining strength above 2,000°C), low thermal expansion, and superior mechanical properties under extreme conditions. Widely used in aerospace components like rocket nozzles, re-entry shields, and aircraft brakes, their Achilles’ heel lies in oxidation vulnerability above 450°C.
C/C coatings refer to specialized surface treatments designed to mitigate oxidation while maintaining thermostructural integrity. At CFCCARBON, our coatings range from glass-phase sealants to multilayer ceramic systems, each engineered for specific temperature thresholds and operational environments.
2. Coating Technologies: Temperature Limits & Innovation Frontiers
2.1 Boron-Based Glass Sealants
Experimental data show B₂O₃ glass layers effectively inhibit oxidation below 1,000°C by forming protective barriers. However, volatilization accelerates above this threshold, with vapor pressure reaching 10⁻¹ MPa in humid environments. When combined with oxide particle binders (e.g., SiC/Si₃N₄), protection extends to 1,200°C through crack-sealing mechanisms7.
Critical limitations emerge at 1,575°C due to CO-induced glass disruption and boron-silicon interfacial corrosion. CFCCARBON’s solution employs graded SiC/B₄C interlayers to buffer thermal stresses, enhancing durability in hypersonic vehicle leading edges.
2.2 Silicon Carbide/Nitride Systems
Pure CVD SiC coatings demonstrate remarkable performance up to 1,700-1,800°C under oxidative conditions. The protective SiO₂ layer
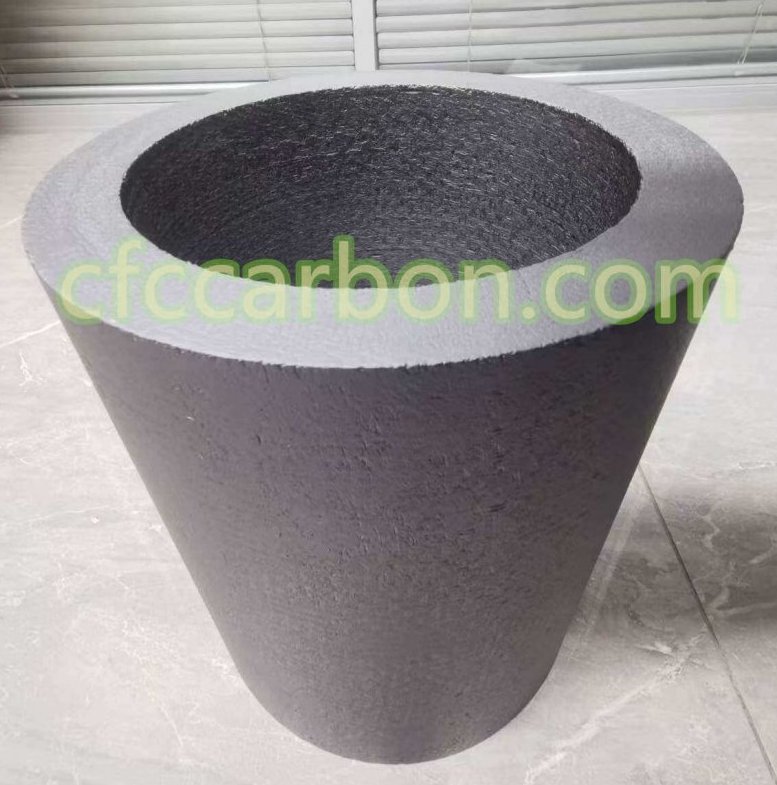
SiC coating carbon fiber composite material-CC-CFC (2)
degrades when CO/N₂ interfacial pressures exceed 10⁻¹ MPa, triggering active oxidation and SiO gas formation. In reduced oxygen environments, failure temperatures drop to 1,500-1,600°C.
Our latest R&D at CFCCARBON integrates Al₂O₃-based thermal barrier coatings (TBCs) with SiC matrices. Testing reveals 1.45mm TBCs reduce CFRP surface temperatures by 60% under 700°C flames while preserving 50% flexural strength post-thermal shock.
3. Manufacturing Breakthroughs: From Preforms to Functionally Graded Materials
The production of oxidation-resistant C/C composites involves three stages:
-
Preform Engineering: Multidirectional carbon fiber architectures (2D, 3D, 4D) are tailored for load distribution4.
-
Matrix Densification: Chemical Vapor Infiltration (CVI) and liquid polymer pyrolysis create dense carbon matrices.
-
Coating Deposition: PGCVI (Pressure Gradient CVI) enables uniform SiC/TaC multilayer coatings on complex geometries like rocket nozzle throats.
CFCCARBON’s 4D composites achieve 1.9g/cm³ density through HIP-assisted pitch densification, offering 30% higher thermal conductivity than conventional 2D laminates.
4. Industrial Applications & Custom Solutions
Application | Coating Type | Temperature Range | Key Advantage |
---|---|---|---|
Spacecraft TPS | SiC-ZrB₂ Graded | 1,800°C+ | Ablation resistance |
Aircraft Brakes | B₄C-SiC Hybrid | 800-1,200°C | Wear reduction by 40% |
Semiconductor Furnaces | Pyrolytic Graphite | 2,500°C | Isothermal uniformity |
Our 3D C/C insulation barrels with resin-impregnated graphite liners now dominate solar furnace markets, achieving <0.5% porosity through proprietary resin infusion techniques.
5. Future Directions: Self-Healing & Nanocomposite Coatings
Emerging technologies address coating limitations:
-
Microencapsulated B₂O₃: Autonomous crack sealing during thermal cycling
-
Graphene-Reinforced TBCs: 200% improvement in interfacial toughness vs conventional Al₂O
-
CNT-Enhanced Matrices: 3D woven preforms with in-situ grown nanotubes reduce delamination during drilling
CFCCARBON’s R&D pipeline includes AI-driven coating thickness optimization algorithms, projected to cut production costs by 25% by 2027.
6. Technical Specifications & Customization
Explore CFCCARBON’s product portfolio:
-
Density Options: 1.4-1.9g/cm³ (Standard to High-Density Grades)
-
Fiber Architectures: 2D Plain Weave, 3D Orthogonal, 4D Cylindrical Preforms
-
Coating Services: CVD SiC, PIP Si₃N₄, Hybrid TBCs with ZrO₂/Y₂O₃
Visit www.cfccarbon.com/products for technical datasheets and OEM customization guides.
related news /articles:
The use of a barrier coating on carbon-carbon composite
Advanced Protective Coatings for Carbon-Carbon Composites
Introduction of high-temperature coatings on CC composite material
Innovations in Carbon-Carbon Composite Internal Coatings