The widespread use of heat exchangers in the chemical industry is well known. The problems that arise while using such equipment are also well known. One of the most prevalent engineering problems is the cleaning of deposits from the inner surfaces of heat exchanger pipes. Deposits in industrial heat exchanger on the water side usually contain minerals such as calcium and magnesium carbonates, along with other salts and corrosive products. These deposits are harder than concrete and pose serious removal problems. This is why the problem of heat exchanger pipe cleaning persists.
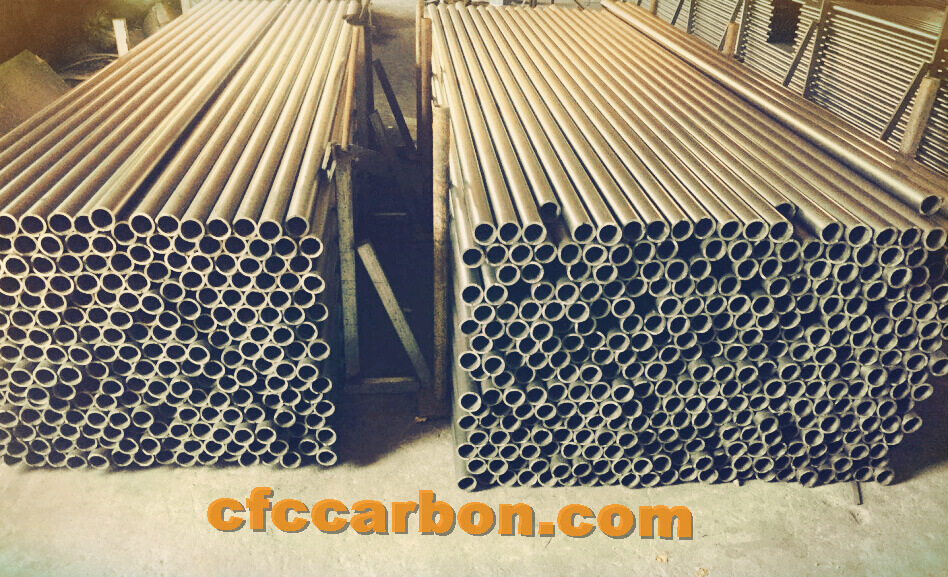
resin graphite pipes for heat exchangers-8
Various cleaning methods have been developed to solve this problem. Some of the more popular cleaning methods are chemical or mechanical ones.
The chemical methods used in industry comprise 25% of all the existing methods. These methods consist of the following categories:
- Chemical cleaning solution circulation is probably the most common method. The system is filled with the solution which is then re-circulated by a pump through the system.
- The method of filling and soaking is probably the simplest of all forms of chemical cleaning.
- The stream cleaning method is used when fouling deposits can be removed while the system is in production mode. Its must be determined that damage to the product will not occur when using this method to clean a system.
- In the stream vapor phase method chemical cleaning solvents are introduced into a high pressure steam flow that in directed through the graphite pipes at a controlled rate.
- Foam cleaning is another method used by chemical cleaning companies. Using a foam generator, the cleaning solution is applied to the surface being cleaned.
graphite pipes for heat exchangers (4)
If chemical cleaning is to be used, it is very beneficial to obtain samples of the deposit so that composition can be determined. Based on their chemical analyses, we can choose the most suitable solvents. Deposits may be of an organic or inorganic nature, and the application of a multi-step cleaning procedure may be required. The use of different types of solvents provides good results for graphite pipe cleaning.
There are various drawbacks with the chemical methods:
- There are environmental pollution issues.
- For production of the solvents special equipment is required, as well as specially trained staff.
- There is risk of damaging the inner surface of the graphite pipes.
These mechanical methods are frequently used to remove deposits and they give good results, but the time is takes to remove the deposit is very long. These methods do not guarantee complete removal of the deposits and a return to the original state of the graphite pipe surfaces.
We present a mechanical method of cleaning, suitable for cleaning pipelines of different diameters and for various sediment types. But, this method is only applicable when fluid flow is present in the graphite pipe. The main advantages of the proposed method are its simplicity, ease of control over the cleaning element’s force of interaction with the pipe wall, and the ability to restore the surface of the pipe to its original clean state.
During development of the proposed method, forces of impact were created between the cleaning element and the pipe wall. In addition to that, there also exists an elastic deformation of the pipe wall as a result of pressure oscillations of the fluid in the pipe. The influence of such complicated stresses leads to intensive exfoliation of the sediment due to the different values of the modulus of elasticity of the pipe and sediment.
A schematic description of the experimental setup is presented in figure 1.
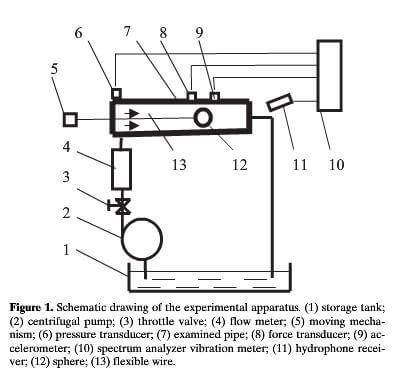
schematic drawing of the experimental apparatus
In some cases, sediment has a variable thickness through the length of the pipe and the inner diameter of the pipe varies significantly. These cases allow another use of the proposed device. Two or three spheres with different diameters can be joined together at specific distances starting with the smallest diameter sphere. Such a scheme is very effective for many polluted pipes. The total mass of rotating elements increases, as does the pressure in the pipe. All this leads to an increase of the force impact on the pipe walls and sediment itself. Complex rotation and impact of the sphere on pipe alls and changes of pressure lead to the intensification of the defoliation process.
This work has succeeded in determining different hydraulic and geometrical parameters affecting force interaction and sphere rotation. This innovative approach for the cleaning of heat exchanger pipes has very good prospects for practical usage.
related news /articles:
Price list of graphite pipes for heat exchangers-2020
Graphite pipes for heat exchangers–Manufacturer in China
Promotion for resin graphite pipes/tubes for heat exchangers