The manufacturing flow sheet in figure 5 shows the main step to manufacture carbon-carbon composite nozzle extensions as of mid of the nineties. Thanks to continuous learning and increasing experience, the maturation of the process has allowed great simplifications so that to decrease significantly the number of manufacturing steps as well as the involved raw materials. The manufacturing flow sheet in figure 6 shows the optimized process as it is now qualified and implemented for production in comparison as it was at the beginning of the development. The economics of C-C nozzle extensions has been improved significantly making this technology a prime candidate to increase the performances of all launchers.

manufacturing process of carbon-carbon nozzle extension
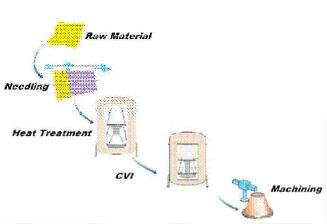
enhanced manufacturing process of carbon-carbon nozzle extension
C-C composite is now currently used for Solid Rocket Motor nozzle throat because its unique capability allowed designing the very high loaded nozzle throat in a single monolithic part.
The P80 which is a 80 metric tons propellant SRM developed for VEGA European small launcher first stage is featuring a Naxeco Sepcarb carbon-carbon nozzle throat. The P80 was successfully ground test fired in November 2006 for development and then ground test fired for qualification in December 2007 with outstanding throat and overall performance, as predicted. See figure 9.
A nozzle has to face very high temperature combustion gas and has to transfer the thrust to the vehicle. Indeed the heat flux and the mechanical load are strongly dependant of the engine type: solid propellant, storage liquid propellant or cryogenic propellant, as well as expansion ratio and other interface requirements.
It appears that lower density, higher diffusivity and low thermal expansion combined with higher temperature capability provide C-C with undeniable advantage for liquid rocket engine Nozzle Extension applications. In particular, C-C nozzle extension weighs twice less and better accommodates thermal mechanical loads than Haynes.
In a second step, it is shown how C-C nozzle extensions comply in a better way than Haynes with usual liquid rocket engine technical and operational requirements.
Moreover, experience shows that the C-C nozzle extension production cycle time of 9 months is shorter than with Haynes. In addition, scraps or critical anomalies have not been experienced with C-C nozzle extensions in production.
Carbon-carbon has been selected for the Vinci deployable nozzle extension. The fixed part of the nozzle extension is attached to the regenerative combustion chamber at a low area ratio. Hence the first section of the nozzle extension has to survive very high temperature, around 1500C, where the combustion gas will be oxidative.
The first C-C/SiC fixed cone has been successfully tested twice in 2008 for a total cumulated duration of 700sec. A temperature of about 1700K has been measured on the outside skin of the cone in the one-third of the height from the flange.
The technology and industrial maturities of C-C proven for rocket motor and engine nozzle applications and available for liquid rocket engine manufacturers in order to help them to reach engine performance objectives by allowing to get very high area ratio with competitive mass and high thermal margins compared to metallic nozzle extension.