The structural geometry of 3D carbon carbon composite fabrics will be discussed according to the four basic methods of textile
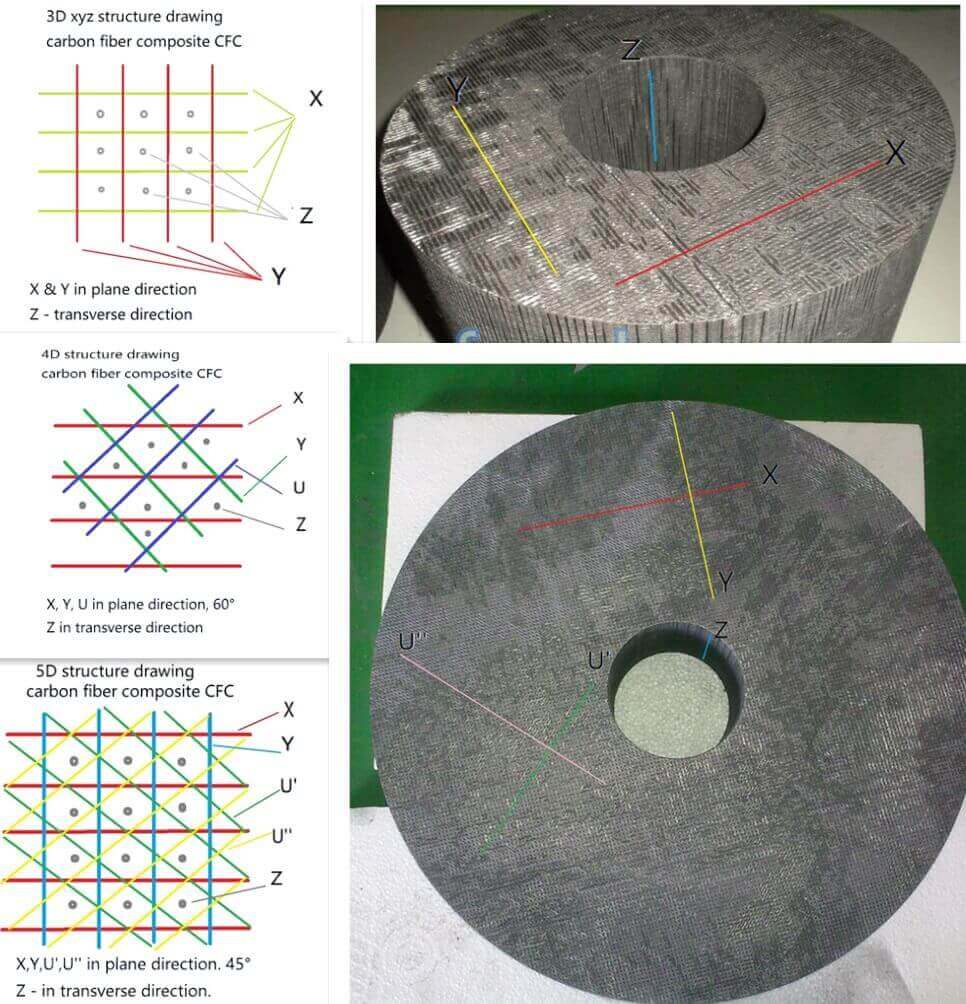
3D4D5D carbon fiber composite CFC structural diagram drawing material (2)
manufacturing: weaving, orthogonal nonwoven, knitting, and braiding.
Knitting 3D fabrics:
The knitted 3D CC composite fabrics are produced either by the weft knitting or warp knitting process. An example of a weft knit is the near-net shape structure knitted under computer control by the pressure foot process. In a collapsed form, this preform has been used for carbon-carbon aircraft brakes.
The unique feature of the weft-knit structures is their conformability. When additional reinforcement is needed in the 0° and 90° directions, linear laid-in yarns can be placed inside the knitting loops. The most undesirable structural reinforcement feature of weft-knit structures is their bulkiness, which leads to the lowest packing density or lowest level of maximum fiber-volume fraction compared with other fabric preforms. Although the weft-knitted structures have applications in limited areas, the multiaxial warp-knit 3D structures are most promising, and they have undergone more development in recent years.
The figure 16(a) and 16(b) show the single bundle XYZ fabrics in a rectangular and cylindrical shape. Figure 16(c)
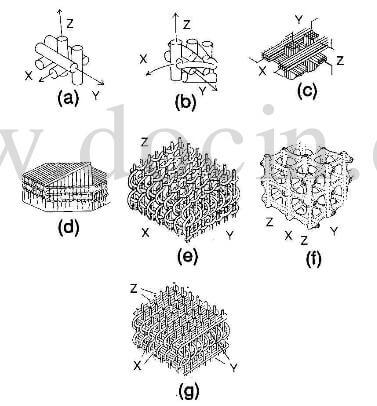
complex structural shapes by 3D braiding
demonstrates the multiple-yarn bundle possibilities in the various directions; figure 16(d) shows the multidirectional reinforcement in the 3D structure plane. Although most of the orthogonal nonwoven 3D structures consist of linear yarn reinforcements in all of the directions, introduction of the planar yarns in a nonlinear manner, as shown in figure 16(e), 16(f), and 16(g), can result in either an open lattice structure or a flexible and conformable structure. cfccarbon.com
3D braided fabrics:
The 3D braiding technology is an extension of the well-established 2D braiding technology wherein the intertwining or orthogonal interlacing of two or more yarn systems to form an integral structure constructs the fabric. The 3D braiding is one of the textile process in which a wide variety of solid complex structural shapes can be produced integrally resulting in a highly damage-resistant structural preform. Figure 21 shows two basic loop setups in circular and rectangular
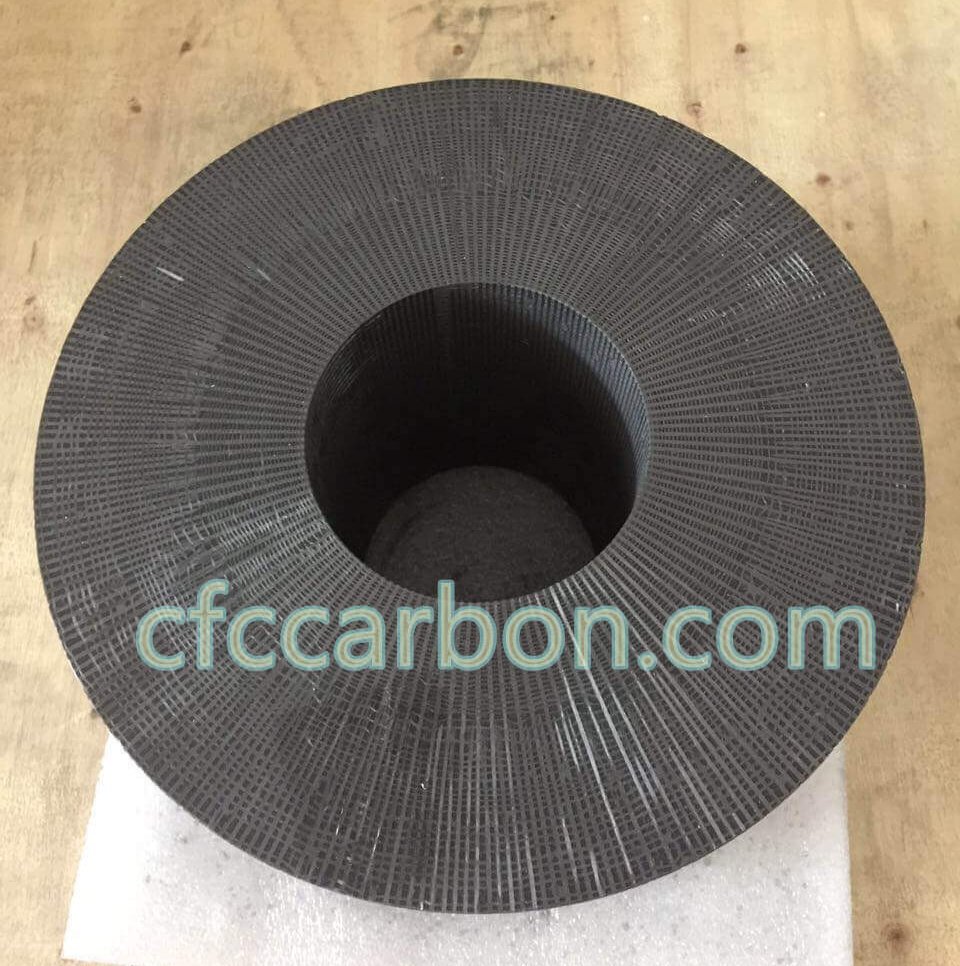
3D 4D 5D Hoops, Loop, weaving, stucture, drawing, carbon fiber, carbon, composite, CFC, CC, manufacturer, China, (1)
configurations. The 3D braids are produced by a number of
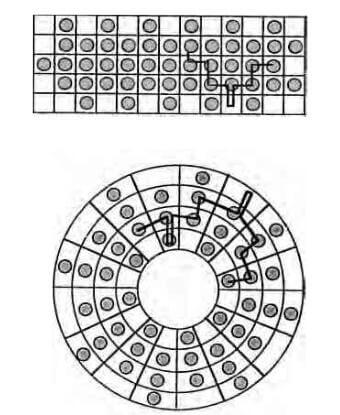
basic loom setups for circular and rectangular configurations.
processes including the Track and Column (3D circular loom) method, the two-step braiding method, and a variety of displacement braiding techniques. The basic braiding motion includes the alternate X and Y displacement of yarn carriers followed by a compacting motion. The proper positioning of the carriers and the joining of various rectangular groups through selected carrier movements accomplish shape formation.
related news /articles:
Structural Geometry of CC composite 2D fabrics (2)—Knitted fabrics and Braided fabrics
carbon fiber reinforcement and architecture-woven 3D fabrics
Different structures of 3D carbon carbon composite | C/C composite
3D Carbon fiber composite | CFC material manufacturer in China